How Can You Successfully Sublimate on Wood?
Sublimation on wood is a fascinating process that combines creativity and technology, allowing you to transform plain wooden surfaces into vibrant, personalized works of art. Whether you’re looking to create custom home decor, unique gifts, or promotional items, sublimation opens up a world of possibilities. This technique not only enhances the aesthetic appeal of wood but also ensures that your designs are long-lasting and resistant to fading. If you’ve ever wondered how to bring your artistic visions to life on wood, you’re in the right place!
At its core, sublimation is a printing process that uses heat to transfer dye onto a variety of materials, including specially coated wood. The magic happens when the dye turns into gas and permeates the surface, creating a stunning, permanent bond. This method is particularly popular among crafters and small business owners who seek to add a personal touch to their projects. However, achieving the best results requires an understanding of the materials and techniques involved, as well as the right equipment.
In this article, we’ll explore the essential steps and considerations for successfully sublimating on wood. From selecting the appropriate wood type to preparing your designs and using the right tools, we’ll guide you through the process to ensure that your sublimation projects turn out beautifully. Whether you’re a seasoned
Choosing the Right Wood for Sublimation
Selecting the appropriate type of wood is crucial for achieving optimal results in sublimation printing. Not all wood surfaces are created equal, and some will yield better results than others. Here are key factors to consider:
- Type of Wood: Plywood, MDF (Medium Density Fiberboard), and specially coated wood are preferred choices. Natural wood surfaces can be used but may require a coating for better adhesion of sublimation dyes.
- Surface Finish: A smooth, even surface allows for better transfer of the sublimation ink. Look for wood that is sanded down and free of imperfections.
- Coating: Some wood products come pre-coated with a polymer layer designed specifically for sublimation. This coating helps in transferring the image effectively.
Preparing the Wood Surface
Before beginning the sublimation process, proper preparation of the wood surface is essential. This step will enhance the quality of the final print.
- Cleaning: Ensure the wood surface is free from dust, grease, or any contaminants. A clean microfiber cloth can be used to wipe the surface.
- Sanding (if necessary): If the wood is rough, lightly sand it using fine-grit sandpaper to create a smoother surface. Be cautious not to damage the wood.
- Applying a Coating: For natural wood, apply a sublimation-friendly coating or use pre-coated wood. This will facilitate better ink absorption.
Printing the Design
Once the wood is prepared, the next step involves printing your design onto sublimation paper.
- Design Software: Use graphic design software to create or modify your image. Ensure the image is in the correct size and resolution, typically 300 DPI for high-quality prints.
- Mirror Image: Remember to mirror your image before printing. This ensures that the final output appears correctly when transferred onto the wood.
- Printer Settings: Set your printer to the appropriate settings for sublimation ink. Use the highest quality print settings and select the correct paper type.
Sublimation Process
The sublimation process requires careful handling to ensure the design transfers accurately onto the wood.
- Heat Press Setup: Preheat your heat press to the recommended temperature, usually between 380°F to 400°F (193°C to 204°C).
- Time and Pressure: Set the timer for about 60 to 120 seconds depending on the thickness of the wood and the heat press model. Apply firm, even pressure.
- Transfer: Align the printed sublimation paper onto the wood surface. Secure it with heat-resistant tape to prevent shifting during the process.
Parameter | Recommended Value |
---|---|
Temperature | 380°F to 400°F (193°C to 204°C) |
Time | 60 to 120 seconds |
Pressure | Firm and even |
Post-Transfer Care
After completing the sublimation process, care is needed to ensure the longevity of the design.
- Cooling: Allow the wood to cool down before handling it. This prevents smudging or damaging the design.
- Sealing (optional): For added protection, consider applying a clear coat or sealant that is compatible with sublimation inks. This can enhance durability against scratches and environmental factors.
- Display and Maintenance: Keep the finished product out of direct sunlight for extended periods and clean with a soft cloth to maintain the quality of the print.
Materials Required for Sublimation on Wood
To achieve optimal results when sublimating on wood, specific materials are essential. The following list outlines the necessary components:
- Sublimation Printer: A printer that uses sublimation ink.
- Sublimation Paper: Special paper designed to hold sublimation ink.
- Wood Blanks: Pre-coated wood specifically prepared for sublimation.
- Heat Press Machine: A flat heat press that can evenly distribute heat and pressure.
- Protective Paper: To prevent ink transfer to the heat press.
- Heat-resistant Tape: To secure the sublimation paper to the wood.
- Heat Gloves: For safe handling of hot materials.
Preparing the Wood for Sublimation
Proper preparation of the wood is crucial for successful sublimation. Follow these steps:
- Select Quality Wood Blanks: Choose wood that has been coated with a polymer coating suitable for sublimation.
- Clean the Surface: Ensure the wood surface is free from dust, grease, and debris. Use a lint-free cloth for this purpose.
- Measure and Cut: If necessary, cut the wood to the desired size before sublimation.
Designing the Artwork
Creating or selecting the right design is an important step in the sublimation process. Consider the following:
- Design Software: Utilize programs like Adobe Illustrator or CorelDRAW to create your artwork.
- Image Resolution: Ensure the image has a high resolution (300 DPI is recommended).
- Color Management: Use RGB color mode to avoid color mismatches during printing.
- Mirror Image: Always mirror your design before printing on sublimation paper to ensure correct orientation.
Printing the Design
Follow these guidelines for printing your design on sublimation paper:
- Printer Setup: Ensure the sublimation printer is properly set up and has sublimation ink installed.
- Paper Settings: Use the appropriate settings for sublimation paper in the printer settings.
- Print Test: Conduct a test print to check for color accuracy and alignment.
Heat Pressing the Design onto Wood
The pressing process is critical for transferring the design onto the wood effectively. Adhere to these steps:
- Preheat the Heat Press: Set the temperature, typically between 380°F to 400°F, and preheat for about 10-15 minutes.
- Align the Design: Place the sublimation paper with the printed design face down on the wood blank.
- Secure with Tape: Use heat-resistant tape to hold the paper in place and prevent shifting.
- Press the Wood: Place the wood blank in the heat press and apply pressure for 45 to 60 seconds.
- Remove Carefully: After the timer goes off, carefully lift the press and remove the wood, using heat gloves to avoid burns.
Post-Processing Steps
After sublimation, follow these post-processing steps for the best finish:
- Cooling Time: Allow the wood to cool completely before handling.
- Inspect the Transfer: Check for any imperfections or spots where the design did not transfer correctly.
- Finishing Touches: If desired, apply a clear sealant or varnish to enhance durability and finish.
Common Issues and Troubleshooting
Be aware of potential issues during sublimation and how to address them:
Issue | Solution |
---|---|
Faded Colors | Check ink levels and printer settings. |
Uneven Transfer | Ensure even pressure and proper alignment. |
Ghosting | Use more heat-resistant tape to secure. |
Design Misalignment | Double-check mirroring and layout before printing. |
These steps and considerations will facilitate a successful sublimation process on wood, allowing for high-quality and durable results.
Expert Insights on Sublimation Techniques for Wood
Dr. Emily Carter (Materials Scientist, Sublimation Innovations Inc.). “Sublimation on wood requires careful preparation of the surface to ensure optimal adhesion of the sublimation ink. Sanding the wood to a fine finish and applying a suitable polymer coating can significantly enhance the quality of the transfer.”
Mark Thompson (Creative Director, Artisan Print Solutions). “Understanding the temperature and pressure settings of your heat press is crucial. For wood sublimation, I recommend a heat setting between 385°F to 400°F and a pressure of around 40-60 psi to achieve vibrant and durable prints.”
Lisa Chen (Owner, Custom Sublimation Co.). “Choosing the right type of wood is essential for successful sublimation. I find that using MDF or specially coated wood products yields the best results, as they are designed to absorb the sublimation ink effectively.”
Frequently Asked Questions (FAQs)
What materials are needed for sublimation on wood?
To successfully sublimate on wood, you will need sublimation paper, sublimation ink, a heat press, a blank wood surface that has been treated for sublimation, and heat-resistant tape.
Can any type of wood be used for sublimation?
Not all wood types are suitable for sublimation. It is best to use specially coated or treated wood that is designed for sublimation, as it allows for better ink transfer and vibrant colors.
How do I prepare wood for sublimation?
Prepare the wood by ensuring it is clean and free from dust or oils. If using untreated wood, apply a sublimation coating to create a suitable surface for the ink to adhere to.
What temperature and time settings should I use for sublimation on wood?
Typically, sublimation on wood requires a temperature of around 385°F to 400°F (196°C to 204°C) and a pressing time of 60 to 120 seconds, depending on the thickness and type of wood.
Can I use a regular inkjet printer for sublimation on wood?
No, a regular inkjet printer cannot be used for sublimation. You must use a printer specifically designed for sublimation that utilizes sublimation ink for proper results.
What are common issues encountered when sublimating on wood?
Common issues include uneven transfer, fading colors, and ghosting. These problems can often be mitigated by ensuring proper temperature, pressure, and using the correct sublimation materials.
sublimation on wood is a unique and innovative process that allows for the transfer of vibrant images onto wooden surfaces. The process involves using sublimation inks and specially coated wood products that can withstand the heat and pressure required for sublimation. Proper preparation of the wood, including ensuring it is clean and free of any contaminants, is essential for achieving high-quality results. Additionally, using the correct temperature and pressure settings during the sublimation process is crucial to ensure that the images adhere properly and maintain their integrity over time.
Key takeaways from the discussion on sublimation on wood include the importance of selecting the right materials, such as sublimation-ready wood or wood that has been coated with a polymer layer. Understanding the equipment needed, such as a heat press and sublimation printer, is also vital for success. Furthermore, experimenting with different designs and techniques can lead to unique and personalized wooden products, making sublimation a versatile option for crafters and businesses alike.
Overall, sublimation on wood opens up a world of creative possibilities. With the right tools and techniques, individuals can produce stunning, customized wooden items that are both functional and aesthetically pleasing. As the sublimation process continues to evolve, staying informed about new materials and methods
Author Profile
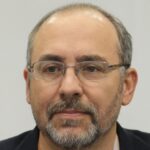
-
Mahlon Boehs is a seasoned entrepreneur and industry expert with a deep understanding of wood truss manufacturing and construction materials. As the President of Timberlake TrussWorks, LLC, Mahlon played a pivotal role in shaping the company’s reputation for quality and precision. His leadership ensured that each truss met rigorous structural standards, providing builders with dependable components essential to their projects.
Beginning in 2025, Mahlon Boehs has shifted his focus to education and knowledge-sharing through an informative blog dedicated to wood truss manufacturing. Drawing from his extensive experience in the field, he provides in-depth insights into truss design, material selection, and construction techniques. This blog serves as a valuable resource for builders, contractors, and homeowners seeking practical guidance on truss systems and structural integrity.
Latest entries
- March 18, 2025General Wood TopicsWhat Color Is Ebony Wood? Unveiling the Rich Hues of This Luxurious Timber
- March 18, 2025Construction & FrameworkHow Can You Effectively Mount a Headboard to Your Wall?
- March 18, 2025General Wood TopicsCan Bees Really Eat Wood? Unraveling the Myths and Facts
- March 18, 2025General Wood TopicsDo Rabbits Really Chew on Wood? Exploring Their Eating Habits!