How Can You Master the Art of Wood Engraving?
Wood engraving is an age-old craft that transforms simple pieces of timber into stunning works of art. Whether you’re looking to personalize a gift, create a unique home decor item, or explore a new hobby, mastering the art of wood engraving can be both rewarding and fulfilling. This intricate technique combines creativity with precision, allowing artisans to carve intricate designs and patterns into wood surfaces. In this article, we will guide you through the essentials of wood engraving, from selecting the right tools to mastering various techniques, ensuring you have everything you need to bring your artistic visions to life.
Wood engraving is not just about the tools and materials; it’s also about understanding the wood itself. Different types of wood exhibit unique characteristics that can affect the engraving process, influencing everything from the depth of the cut to the final appearance of the design. As you embark on this journey, you’ll discover how to choose the right wood for your project, which can greatly enhance the overall outcome.
Moreover, the engraving process itself can vary widely, encompassing various techniques that cater to different styles and skill levels. From traditional hand tools to modern power tools, each method offers its own set of challenges and rewards. As you delve deeper into the world of wood engraving, you’ll learn how to develop your skills, experiment with
Tools Required for Wood Engraving
To begin the wood engraving process, it is essential to have the right tools at your disposal. The choice of tools can significantly affect the quality and precision of your work. Below is a list of common tools used in wood engraving:
- Engraving Tools: These can include rotary tools, wood chisels, or engraving knives. Each type offers varying levels of detail and control.
- Dremel or Rotary Tool: Ideal for detailed work, especially in intricate designs.
- Wood Carving Knives: Used for deeper cuts and shaping the wood.
- Burning Tool: A pyrography tool can be used to burn designs into the wood surface.
- Sandpaper: Necessary for smoothing the surface before and after engraving.
- Clamps: To secure the wood piece while working.
- Safety Gear: Goggles and dust masks are essential to protect against debris and dust.
Preparing Your Wood
Before beginning the engraving process, proper preparation of the wood surface is crucial. This ensures that the engraving adheres well and enhances the final appearance.
- Select the Right Wood: Softer woods like pine or basswood are often easier to engrave, while hardwoods such as oak may require more effort.
- Sanding the Surface: Use fine-grit sandpaper to smooth out the wood surface. This helps achieve cleaner cuts and a finer finish.
- Applying a Base Coat: If desired, apply a base coat of paint or wood stain to enhance the contrast of the engraving.
- Tracing the Design: Use carbon paper or a transfer method to outline your design on the wood surface.
Wood Type | Characteristics | Best For |
---|---|---|
Pine | Soft, easy to carve | Beginners, detailed work |
Birch | Fine grain, slightly harder | Intermediate projects |
Oak | Hard, durable | Advanced carving, intricate designs |
Basswood | Soft, smooth texture | All skill levels, versatile use |
Techniques for Wood Engraving
Engraving techniques vary based on the tools used and the desired outcome. Understanding these techniques can help in achieving a professional-looking finish.
- Hand Engraving: Using chisels or carving knives, this technique requires a steady hand and skill to achieve fine detail.
- Power Engraving: Utilizing a rotary tool allows for faster work and the ability to create intricate designs with less physical effort.
- Pyrography: This technique involves burning designs into the wood with a heated tool. It is excellent for creating shading and textures.
- Relief Engraving: Involves removing the wood around the design, leaving the design raised above the surface.
Practicing different techniques on scrap wood can help develop skills and confidence before moving to your final piece.
Choosing the Right Tools for Wood Engraving
Selecting appropriate tools is crucial for achieving precise wood engraving. The primary tools include:
- Dremel Tool: Versatile rotary tool for detailed designs.
- Wood Engraving Pens: These provide excellent control for intricate work.
- Laser Engraver: Ideal for precise and complex patterns, suitable for advanced users.
- Chisels and Gouges: Traditional tools for hand carving, requiring skill and practice.
When choosing tools, consider the type of wood and the desired intricacy of the design. Softer woods like pine are easier to engrave, while hardwoods like oak require sharper tools and more effort.
Preparing Your Workspace
A well-organized workspace enhances productivity and safety. Follow these guidelines:
- Clean Surface: Ensure your workbench is clear of clutter.
- Proper Lighting: Use bright, adjustable lighting to illuminate your project.
- Safety Equipment: Wear safety goggles and a dust mask to protect against debris.
- Ventilation: Ensure good airflow, especially when using power tools or lasers.
Designing Your Engraving
Creating a design is fundamental to wood engraving. Consider these steps:
- Sketching the Design: Start with a rough sketch on paper.
- Transferring the Design: Use graphite transfer paper to outline on wood.
- Choosing Patterns: Select between geometric shapes, floral designs, or personalized text.
- Digital Design: For precision, software like Adobe Illustrator can be utilized to create vector designs.
Engraving Techniques
Different techniques yield various effects in wood engraving. Key methods include:
- Outline Engraving: Focusing on the borders of the design.
- Shading: Using varying depths and patterns to create shadow effects.
- Relief Engraving: Carving away the background to make the design stand out.
The choice of technique depends on the desired outcome and the complexity of the design.
Wood Selection Considerations
The type of wood affects both the engraving process and final appearance. Common woods used include:
Wood Type | Characteristics | Best For |
---|---|---|
Pine | Soft, easy to carve | Beginners, simple designs |
Birch | Moderate hardness, fine grain | Detailed engravings |
Oak | Hard, durable, distinct grain | Complex patterns |
Maple | Hard, smooth surface | Precision work |
Cedar | Aromatic, lightweight | Decorative items |
Choose wood based on your project requirements and your skill level.
Finishing Techniques
After engraving, finishing enhances appearance and protects the wood. Consider these options:
- Sanding: Smooth the surface with fine-grit sandpaper to remove splinters.
- Staining: Apply wood stain to enhance color while highlighting the engraving.
- Sealing: Use a clear finish or sealant to protect against moisture and wear.
Each finishing method should be tested on a scrap piece of wood to ensure compatibility.
Expert Insights on Wood Engraving Techniques
Emily Carter (Master Woodworker, Artisan Crafts Journal). “To successfully wood engrave, one must first select the right type of wood. Softwoods like pine are easier to carve but may not hold fine details as well as hardwoods like maple or cherry. Proper tool selection is also crucial; using sharp chisels and a steady hand can significantly enhance the quality of your engravings.”
James Thompson (Woodworking Instructor, Craftsmanship School). “Understanding the grain of the wood is essential when engraving. Engraving against the grain can lead to splintering, while following it allows for smoother cuts. Additionally, practicing on scrap pieces before working on your final project can help refine your technique and boost your confidence.”
Linda Martinez (Artistic Designer, Wood & Craft Magazine). “Incorporating various techniques such as pyrography alongside traditional engraving can create stunning effects. Experimenting with different tools, like rotary engravers or laser cutters, can also expand your creative possibilities, allowing you to achieve intricate designs that are not possible with hand tools alone.”
Frequently Asked Questions (FAQs)
What tools are needed for wood engraving?
To engrave wood, you typically need a wood engraving tool or a rotary tool with engraving bits, a steady work surface, clamps to secure the wood, and safety gear such as goggles and a dust mask.
What types of wood are best for engraving?
Softwoods like pine and cedar are ideal for beginners due to their ease of engraving. Hardwoods like oak and maple can also be engraved but require more skill and appropriate tools.
How do I prepare wood for engraving?
Begin by sanding the wood surface to a smooth finish, removing any dust or debris. Optionally, apply a wood conditioner to ensure an even engraving result.
Can I use a laser engraver for wood engraving?
Yes, laser engravers are highly effective for wood engraving, allowing for intricate designs and precise detailing. Ensure the wood is suitable for laser engraving to avoid burning.
What techniques can I use for wood engraving?
Common techniques include line engraving, shading, and stippling. Each technique produces different visual effects, so practice is essential to achieve desired results.
How do I maintain my engraving tools?
Regularly clean your tools to remove resin and debris. Keep blades sharp for optimal performance, and store them in a dry place to prevent rust and damage.
wood engraving is a meticulous art form that combines creativity with technical skill. The process begins with selecting the right type of wood, as different woods yield varying results in terms of texture and detail. Tools such as engraving knives, chisels, and rotary tools are essential for achieving precision in designs. Understanding the techniques of carving, shading, and finishing is crucial for producing high-quality engravings that enhance the natural beauty of the wood.
Additionally, preparation plays a significant role in the engraving process. Properly preparing the wood surface by sanding and applying a suitable finish can greatly affect the outcome of the engraving. Artists should also consider the design layout, as planning the composition beforehand can help in executing the engraving more efficiently. Experimentation with different techniques and styles can lead to unique results, allowing for personal expression in each piece.
Ultimately, wood engraving requires patience and practice. As with any craft, developing proficiency takes time, but the rewards are evident in the intricate and beautiful pieces that can be created. Engravers should continuously seek to improve their skills and explore new methods, as this will not only enhance their artistry but also contribute to the evolution of the craft itself.
Author Profile
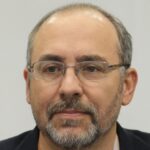
-
Darryl Norman is a seasoned entrepreneur and industry expert with a deep understanding of wood truss manufacturing and construction materials. As the President of Timberlake TrussWorks, LLC, Darryl played a pivotal role in shaping the company’s reputation for quality and precision. His leadership ensured that each truss met rigorous structural standards, providing builders with dependable components essential to their projects.
Beginning in 2025, Darryl Norman has shifted his focus to education and knowledge-sharing through an informative blog dedicated to wood truss manufacturing. Drawing from his extensive experience in the field, he provides in-depth insights into truss design, material selection, and construction techniques. This blog serves as a valuable resource for builders, contractors, and homeowners seeking practical guidance on truss systems and structural integrity.
Latest entries
- March 18, 2025General Wood TopicsWhat Color Is Ebony Wood? Unveiling the Rich Hues of This Luxurious Timber
- March 18, 2025Construction & FrameworkHow Can You Effectively Mount a Headboard to Your Wall?
- March 18, 2025General Wood TopicsCan Bees Really Eat Wood? Unraveling the Myths and Facts
- March 18, 2025General Wood TopicsDo Rabbits Really Chew on Wood? Exploring Their Eating Habits!