How Are Wood Veneers Made? Unveiling the Craftsmanship Behind This Timeless Material
Wood veneers have long been cherished for their beauty and versatility, gracing everything from fine furniture to intricate cabinetry. These thin slices of wood, often crafted from some of the most exquisite tree species, offer a sustainable way to showcase the natural elegance of wood without the hefty price tag associated with solid lumber. But how exactly are these delicate sheets created? Understanding the process behind wood veneer production not only enhances our appreciation for this material but also reveals the craftsmanship and technology that bring it to life. In this article, we will delve into the fascinating journey of wood veneers, from the forest to the finished product, uncovering the techniques and artistry involved in their creation.
The process of making wood veneers begins with selecting the right logs, which are chosen for their grain patterns and overall quality. Once harvested, these logs undergo a series of steps, including debarking and cutting, to prepare them for slicing. The method of slicing can vary, employing techniques such as rotary cutting or flat slicing, each yielding distinct visual characteristics in the final veneer. The thickness of the veneer is crucial, as it must balance durability with the ability to showcase the wood’s natural beauty.
After slicing, the veneers are dried and treated to enhance their stability and longevity. This stage is vital, as it
Selection of Raw Materials
The creation of wood veneers begins with the careful selection of raw materials. High-quality logs are essential for producing veneers that meet both aesthetic and functional requirements. Factors influencing the choice of wood include species, grain patterns, and color. Commonly used species include:
- Oak
- Maple
- Cherry
- Walnut
- Birch
The logs are inspected for defects, ensuring that only the best timber is utilized in the veneer-making process.
Preparation of Logs
Once the logs are selected, they are prepared for slicing. This involves several steps:
- Debarking: The outer bark is removed to expose the clean wood underneath.
- Cutting to Length: Logs are cut into manageable lengths based on the desired veneer size.
- Soaking or Steaming: The logs may be soaked in water or steamed to soften the wood fibers, making them easier to slice.
This preparation is crucial, as it impacts the quality and characteristics of the final veneer.
Slicing Techniques
Veneers can be produced using various slicing techniques, each yielding different grain patterns and thicknesses. The primary methods include:
- Rotary Cutting: The log is mounted on a lathe and turned against a knife, producing a continuous sheet of veneer. This method is efficient and ideal for large-scale production.
- Slicing: The log is sliced along its length. This can be done using:
- Flat slicing: Produces a cathedral grain pattern.
- Quarter slicing: Yields a straight grain pattern, enhancing the wood’s natural beauty.
- Sawing: This method uses a saw to cut the log into thinner sheets, which can result in thicker veneers.
The choice of slicing technique depends on the desired aesthetics and application of the veneer.
Drying Process
After slicing, the veneers must be dried to prevent warping and ensure stability. The drying process can be conducted in several ways:
- Air Drying: Veneers are stacked and allowed to dry naturally in a controlled environment.
- Kiln Drying: Veneers are placed in a kiln to accelerate the drying process. This method is more efficient and helps reduce moisture content uniformly.
The moisture content of the veneer is critical for its performance in various applications, particularly in furniture making and cabinetry.
Finishing and Grading
Once dried, veneers undergo finishing processes that may include sanding, staining, and sealing. The goal is to enhance the wood’s natural beauty while providing protection against wear and environmental factors.
Grading of veneers is also performed at this stage, categorizing them based on quality, appearance, and defects. Common grades include:
- A Grade: High-quality veneers with minimal defects.
- B Grade: Good quality with some allowable defects.
- C Grade: Lower quality, suitable for more utilitarian applications.
The final grading affects the veneer’s market value and its suitability for various projects.
Grading | Description | Typical Uses |
---|---|---|
A Grade | Minimal defects, exceptional appearance | High-end furniture, cabinetry |
B Grade | Some defects, good appearance | Standard furniture, decorative applications |
C Grade | Noticeable defects, functional | Utility applications, budget projects |
This meticulous process ensures that wood veneers are not only visually appealing but also durable and functional for a variety of applications.
Raw Material Selection
The quality of wood veneers begins with the selection of raw materials. Various species of trees are chosen based on their characteristics, availability, and intended use. Key factors in selection include:
- Grain Pattern: Different species exhibit unique grain patterns that influence aesthetics.
- Color: Natural color variations can affect the final appearance of the veneer.
- Density: The hardness and density of wood impact durability and workability.
- Sustainability: Preference is often given to sustainably sourced timber to minimize environmental impact.
Log Preparation
Once the appropriate wood species is selected, logs undergo a series of preparation steps:
- Debarking: The outer bark of the logs is removed to expose the wood.
- Soaking: Logs are often soaked in water or steam to soften the wood, making it easier to slice.
- Cutting: Logs are cut into manageable lengths, typically 8 to 12 feet, depending on the desired veneer size.
Veneer Cutting Techniques
The method of cutting veneers significantly influences their quality and characteristics. Common cutting techniques include:
- Rotary Cutting: The log is mounted on a lathe and turned against a knife, producing a continuous sheet of veneer. This technique maximizes yield but may produce varying grain patterns.
- Slicing: Logs are sliced into veneers using a straight knife. This method results in thicker veneers and more consistent grain patterns. Variants include:
- Flat Slicing: Produces a cathedral grain pattern, popular in furniture making.
- Quarter Slicing: Yields a straighter grain, often used in high-end applications.
- Sawing: Involves cutting logs into thinner sheets with a saw. This method is less common for veneers but can create unique textures.
Drying Process
After cutting, veneers must be dried to prevent warping and cracking:
- Air Drying: Veneers are stacked and allowed to dry in a controlled environment. This method can take weeks.
- Kiln Drying: Veneers are placed in a kiln where heat and humidity are regulated to expedite drying. This method ensures consistent moisture content and reduces drying time.
Finishing Treatments
Once dried, veneers may undergo additional treatments to enhance their appearance and durability:
- Sanding: Surfaces are sanded to achieve a smooth finish, ready for finishing applications.
- Staining: Veneers can be stained to enhance color and highlight grain patterns.
- Sealing: A sealant is applied to protect the wood and enhance longevity.
Quality Control
Throughout the production process, quality control measures are implemented to ensure the final product meets industry standards:
Criteria | Inspection Method | Acceptable Standard |
---|---|---|
Thickness | Caliper measurement | ±0.1 mm |
Moisture Content | Moisture meter | 6-8% |
Surface Defects | Visual inspection | Minimal visible imperfections |
Packaging and Distribution
Finally, once the veneers pass quality control, they are packaged for distribution. Proper packaging is crucial to prevent damage during transport. Common practices include:
- Stacking: Veneers are stacked with protective sheets in between to avoid scratching.
- Wrapping: Use of shrink wrap or cardboard to secure and protect the veneers.
- Labeling: Each package is labeled with species, thickness, and other relevant information for easy identification.
The careful processes involved in creating wood veneers ensure that they meet the needs of various applications, from cabinetry to fine furniture.
Understanding the Process of Wood Veneer Production
Dr. Emily Carter (Wood Technology Specialist, Timber Innovations Institute). “The production of wood veneers begins with the careful selection of high-quality logs. These logs are then debarked and cut into manageable lengths before being subjected to either rotary peeling or slicing, which determines the grain pattern and thickness of the veneer.”
Mark Thompson (Furniture Designer and Woodworking Expert, Artisan’s Journal). “After the initial cutting, the veneers undergo a drying process to reduce moisture content, which is crucial for preventing warping and ensuring a smooth finish. This step is often overlooked but is essential for achieving the desired quality in the final product.”
Linda Nguyen (Sustainability Consultant, EcoWood Solutions). “Sustainability plays a pivotal role in modern veneer production. Many manufacturers now prioritize sourcing logs from responsibly managed forests and utilize eco-friendly adhesives during the lamination process, aligning with global sustainability goals.”
Frequently Asked Questions (FAQs)
How are wood veneers produced?
Wood veneers are produced by slicing or peeling thin layers from a log of wood. This process involves using specialized machinery that can create uniform sheets of veneer, which are then dried and prepared for various applications.
What types of wood are commonly used for veneers?
Common types of wood used for veneers include oak, maple, cherry, walnut, and mahogany. Each type offers distinct grain patterns and colors, catering to different aesthetic preferences and design needs.
What is the difference between sliced and rotary cut veneers?
Sliced veneers are cut from the log in a way that preserves the grain pattern, resulting in a more natural appearance. Rotary cut veneers are produced by rotating the log against a blade, creating a continuous sheet that often exhibits a more uniform grain but less detail.
How are wood veneers treated after cutting?
After cutting, wood veneers undergo a drying process to reduce moisture content, which helps prevent warping and cracking. They may also be treated with adhesives or finishes to enhance durability and appearance.
Can wood veneers be used for both furniture and cabinetry?
Yes, wood veneers are versatile and can be used for both furniture and cabinetry. They provide an attractive finish while being more cost-effective than solid wood, allowing for a wide range of design options.
What are the environmental benefits of using wood veneers?
Using wood veneers is more sustainable than solid wood, as it maximizes the use of each log. Veneers allow manufacturers to create beautiful wood surfaces while conserving resources and reducing waste, making them an eco-friendly choice.
Wood veneers are thin slices of wood that are typically less than 3mm thick, crafted from logs through a meticulous process that ensures both aesthetic appeal and structural integrity. The production of wood veneers begins with the selection of high-quality logs, which are then subjected to various methods of slicing or peeling. These methods include rotary cutting, flat slicing, quarter slicing, and rift slicing, each providing distinct grain patterns and characteristics that enhance the visual quality of the final product.
Once the wood is sliced, it undergoes drying to reduce moisture content, which is crucial for preventing warping and ensuring durability. After drying, the veneers are often treated with adhesives or finishes to enhance their appearance and protect against environmental factors. The final step involves careful inspection and grading to ensure that the veneers meet industry standards for quality and consistency before they are packaged and distributed for use in furniture, cabinetry, and other applications.
In summary, the production of wood veneers is a sophisticated process that combines traditional craftsmanship with modern technology. The choice of cutting technique and the quality of the raw material significantly influence the final product, making it essential for manufacturers to adhere to high standards throughout the production process. Understanding these aspects can help consumers appreciate the value and versatility of wood veneers in
Author Profile
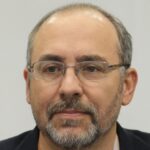
-
Darryl Norman is a seasoned entrepreneur and industry expert with a deep understanding of wood truss manufacturing and construction materials. As the President of Timberlake TrussWorks, LLC, Darryl played a pivotal role in shaping the company’s reputation for quality and precision. His leadership ensured that each truss met rigorous structural standards, providing builders with dependable components essential to their projects.
Beginning in 2025, Darryl Norman has shifted his focus to education and knowledge-sharing through an informative blog dedicated to wood truss manufacturing. Drawing from his extensive experience in the field, he provides in-depth insights into truss design, material selection, and construction techniques. This blog serves as a valuable resource for builders, contractors, and homeowners seeking practical guidance on truss systems and structural integrity.
Latest entries
- March 18, 2025General Wood TopicsWhat Color Is Ebony Wood? Unveiling the Rich Hues of This Luxurious Timber
- March 18, 2025Construction & FrameworkHow Can You Effectively Mount a Headboard to Your Wall?
- March 18, 2025General Wood TopicsCan Bees Really Eat Wood? Unraveling the Myths and Facts
- March 18, 2025General Wood TopicsDo Rabbits Really Chew on Wood? Exploring Their Eating Habits!