Is Steel Frame Construction More Cost-Effective Than Wood?
When it comes to construction, the choice of materials can significantly impact both the budget and the longevity of a project. Among the most debated options are steel frames and traditional wood structures. As builders and homeowners alike seek cost-effective and durable solutions, the question arises: is steel frame cheaper than wood? This inquiry delves into not only the initial costs but also the long-term implications of each material choice. In this article, we will explore the financial, structural, and environmental aspects of steel and wood, helping you make an informed decision for your next building endeavor.
The debate between steel and wood as primary building materials is multifaceted. On one hand, wood has long been favored for its natural aesthetic and ease of use, often coming with a lower upfront cost. However, steel frames are gaining traction due to their strength, resilience, and resistance to common issues such as pests and rot. As construction practices evolve, understanding the economic implications of each material becomes essential for anyone considering a new build or renovation.
In examining whether steel frame construction is indeed cheaper than wood, it’s crucial to consider various factors beyond just material costs. Labor expenses, maintenance requirements, and the potential for energy efficiency all play significant roles in the overall financial picture. As we dive deeper into this topic, we will uncover
Cost Analysis of Steel Frame vs. Wood
When comparing the costs of steel framing and wood framing, several factors come into play. While initial material costs are a significant consideration, other aspects such as labor, longevity, maintenance, and environmental impact must also be considered.
Steel framing typically has higher upfront costs compared to wood. Here’s a breakdown of key cost factors:
- Material Costs:
- Steel framing materials can be more expensive than lumber.
- Prices fluctuate based on market demand and availability.
- Labor Costs:
- Steel framing often requires specialized labor, which may lead to higher labor costs.
- Wood framing is generally easier to work with and can be completed by a broader range of contractors.
- Construction Speed:
- Steel structures can be erected faster, potentially reducing overall labor costs despite higher initial prices.
- Long-Term Costs:
- Steel is resistant to pests, rot, and fire, leading to lower maintenance and replacement costs over time.
- Wood may require treatments and regular maintenance, impacting long-term expenses.
Comparative Cost Table
Cost Factor | Steel Frame | Wood Frame |
---|---|---|
Material Cost per Square Foot | $6 – $15 | $4 – $8 |
Labor Cost per Hour | $50 – $75 | $30 – $50 |
Construction Time (Days) | 10 – 15 | 15 – 30 |
Maintenance Cost (Annual) | $200 – $500 | $300 – $700 |
Durability and Longevity
The longevity of steel frames often exceeds that of wood, which can be susceptible to environmental factors. Steel structures can last for decades with minimal maintenance, while wood may require replacement or significant repairs after 20-30 years, depending on conditions.
- Pest Resistance: Steel is impervious to termites and other pests that can damage wood.
- Weather Resilience: Steel does not warp or swell in response to moisture, maintaining structural integrity over time.
Environmental Considerations
From an environmental perspective, the sustainability of steel and wood varies significantly.
- Steel:
- Often made from recycled materials, steel framing contributes to lower carbon footprints.
- Recyclability at the end of its life cycle is a significant advantage.
- Wood:
- A renewable resource, wood can be sustainably harvested, but deforestation practices can negate this benefit.
- The carbon storage capacity of wood contributes positively to environmental impact if sourced responsibly.
Evaluating whether steel frame construction is cheaper than wood involves a comprehensive analysis of both immediate and long-term costs, alongside durability and environmental factors. The choice ultimately depends on project specifics, budget constraints, and desired longevity.
Cost Comparison of Steel Frame and Wood Construction
The cost of construction using steel frames versus wood can vary significantly based on several factors, including material prices, labor costs, and project specifications. Understanding these elements is essential for making an informed decision.
Material Costs
Material costs play a crucial role in the overall budget of a construction project. Here’s a breakdown of average costs associated with each material:
- Steel Frame:
- Average cost per ton: $700 – $1,200
- Availability of recycled steel can influence pricing positively.
- Wood:
- Average cost per board foot: $3 – $7 (depending on the type of wood)
- Prices can fluctuate based on demand, species, and regional availability.
Material Type | Average Cost Range |
---|---|
Steel Frame | $700 – $1,200 per ton |
Wood | $3 – $7 per board foot |
Labor Costs
Labor costs can also differ between steel frame and wood construction due to the skill level required and the time taken for installation.
- Steel Frame:
- Requires specialized labor, often leading to higher labor costs.
- Installation can be quicker due to the prefabrication of steel components.
- Wood:
- Generally requires less specialized labor, which can reduce costs.
- Traditional building methods may take longer due to cutting and fitting.
Labor Factor | Steel Frame | Wood |
---|---|---|
Skill Level | High | Moderate |
Installation Time | Faster | Slower |
Long-term Costs
While initial costs are important, long-term costs must also be considered.
- Maintenance:
- Steel is resistant to pests and rot, potentially leading to lower maintenance costs over time.
- Wood may require regular treatments to prevent termites and decay.
- Energy Efficiency:
- Steel structures can be designed to be highly energy-efficient with proper insulation.
- Wood naturally has better thermal insulation properties, which can lower heating and cooling costs.
Cost Factor | Steel Frame | Wood |
---|---|---|
Maintenance | Lower | Higher |
Energy Efficiency | High | Moderate |
Environmental Impact
The environmental aspects of both materials should also be considered, as they can indirectly affect costs and project feasibility.
- Steel Frame:
- Often made from recycled materials, which can minimize environmental impact.
- Manufacturing steel is energy-intensive, contributing to a larger carbon footprint.
- Wood:
- Renewable resource, potentially offering a lower carbon footprint if sourced sustainably.
- Deforestation concerns can arise depending on sourcing practices.
Environmental Factor | Steel Frame | Wood |
---|---|---|
Renewability | Non-renewable | Renewable |
Carbon Footprint | High | Variable (depends on sourcing) |
When deciding between steel frame and wood construction, it is essential to analyze not only the upfront costs but also the long-term implications and environmental impact. Each material presents unique advantages and drawbacks, making the choice highly dependent on project requirements and priorities.
Comparing Costs: Steel Frame vs. Wood Construction
Emily Carter (Construction Cost Analyst, BuildSmart Consulting). “In many cases, steel framing can be more cost-effective than wood, especially when considering the long-term durability and maintenance costs. While the initial investment for steel may be higher, its resistance to pests and weather-related damage can lead to significant savings over time.”
James Thompson (Structural Engineer, EcoBuild Innovations). “The decision between steel and wood framing often hinges on the specific project requirements. For large commercial structures, steel tends to be cheaper due to its strength and ability to span larger distances without support. However, for smaller residential projects, wood may still be the more economical choice.”
Linda Martinez (Sustainable Building Consultant, GreenFuture Solutions). “While steel framing can offer cost advantages in terms of longevity and sustainability, the initial costs can vary significantly based on market conditions. It is essential to conduct a thorough cost analysis that includes labor, materials, and potential future expenses to determine which option is truly cheaper for your specific project.”
Frequently Asked Questions (FAQs)
Is steel frame construction generally cheaper than wood?
Steel frame construction can be cheaper in certain contexts, particularly for large-scale projects where material efficiency and durability are prioritized. However, initial costs for steel can be higher than wood, depending on market conditions and local availability.
What are the long-term cost implications of using steel versus wood?
Long-term costs for steel can be lower due to its durability, resistance to pests, and lower maintenance requirements. Wood may require more upkeep and replacement over time, potentially increasing overall costs.
How do labor costs compare between steel and wood framing?
Labor costs can vary significantly. Steel framing often requires specialized skills and tools, which may increase labor expenses. Wood framing is generally more straightforward, potentially leading to lower labor costs.
Are there environmental considerations when choosing steel over wood?
Yes, steel is recyclable and can have a lower carbon footprint if sourced sustainably. However, wood is a renewable resource and can also be environmentally friendly if harvested responsibly. The choice may depend on specific project goals and sustainability practices.
What factors influence the cost comparison between steel and wood framing?
Factors include local material prices, project scale, design complexity, labor availability, and regional building codes. Each project may present unique circumstances that affect the overall cost comparison.
Is steel frame construction more suitable for certain types of buildings than wood?
Yes, steel framing is often preferred for commercial buildings, high-rise structures, and areas prone to severe weather. Wood framing is commonly used for residential buildings and smaller structures due to its versatility and ease of construction.
In comparing the costs of steel frame construction to wood frame construction, several factors must be considered. Generally, steel frames tend to have a higher initial material cost than wood. However, this upfront investment can be offset by the long-term benefits of steel, such as durability, lower maintenance costs, and resistance to pests and environmental factors. Additionally, the speed of construction with steel can lead to savings in labor costs, making it a more economical choice in certain scenarios.
Furthermore, the choice between steel and wood may also depend on the specific project requirements, including design, location, and intended use. For example, steel is often favored in commercial construction due to its strength and ability to span large distances without support. On the other hand, wood remains popular in residential projects for its aesthetic appeal and ease of use. Ultimately, the decision should be based on a comprehensive analysis of both the short-term and long-term financial implications.
In summary, while steel frames may be more expensive initially, their longevity and lower maintenance needs can make them a cost-effective option over time. Wood frames, although cheaper upfront, may incur higher costs in maintenance and repairs. Therefore, stakeholders should carefully evaluate their specific needs and budget constraints to determine the most suitable framing material
Author Profile
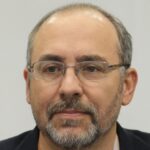
-
Darryl Norman is a seasoned entrepreneur and industry expert with a deep understanding of wood truss manufacturing and construction materials. As the President of Timberlake TrussWorks, LLC, Darryl played a pivotal role in shaping the company’s reputation for quality and precision. His leadership ensured that each truss met rigorous structural standards, providing builders with dependable components essential to their projects.
Beginning in 2025, Darryl Norman has shifted his focus to education and knowledge-sharing through an informative blog dedicated to wood truss manufacturing. Drawing from his extensive experience in the field, he provides in-depth insights into truss design, material selection, and construction techniques. This blog serves as a valuable resource for builders, contractors, and homeowners seeking practical guidance on truss systems and structural integrity.
Latest entries
- March 18, 2025General Wood TopicsWhat Color Is Ebony Wood? Unveiling the Rich Hues of This Luxurious Timber
- March 18, 2025Construction & FrameworkHow Can You Effectively Mount a Headboard to Your Wall?
- March 18, 2025General Wood TopicsCan Bees Really Eat Wood? Unraveling the Myths and Facts
- March 18, 2025General Wood TopicsDo Rabbits Really Chew on Wood? Exploring Their Eating Habits!