Should I Let Pressure Treated Wood Dry Before Installing It?
When embarking on a home improvement project, particularly one involving outdoor structures like decks or fences, the choice of materials can significantly impact both the durability and aesthetics of the final product. Pressure-treated wood is a popular option for its resistance to rot and insects, making it a go-to choice for many DIY enthusiasts and contractors alike. However, a common question arises: should you let pressure-treated wood dry before installation? This seemingly simple query holds the key to ensuring your project stands the test of time and maintains its appeal.
Understanding the properties of pressure-treated wood is essential for any homeowner looking to maximize their investment. Freshly treated wood often contains a significant amount of moisture from the chemicals used in the treatment process, which can affect its performance and longevity if not properly addressed. The decision to allow this wood to dry before installation can influence not just the immediate results of your project, but also its long-term stability and appearance.
As you delve deeper into the considerations surrounding pressure-treated wood, you’ll discover the implications of moisture content on installation techniques, potential warping or shrinking, and the overall effectiveness of your chosen treatment. By weighing the pros and cons of allowing the wood to dry, you can make an informed decision that will enhance the quality and lifespan of your outdoor projects.
Factors Influencing the Drying Time of Pressure Treated Wood
The drying time for pressure treated wood can vary significantly based on several factors. Understanding these can help you determine whether to install it immediately or allow for additional drying time.
- Type of Treatment: Different chemical preservatives and methods can affect the moisture content of the wood.
- Climate Conditions: Humidity and temperature during the drying period play a crucial role. Warmer, drier climates will facilitate faster drying.
- Wood Species: Different species have varying densities and moisture retention properties, influencing how long they take to dry.
- Thickness of the Boards: Thicker boards will retain moisture longer than thinner ones.
Benefits of Allowing Pressure Treated Wood to Dry
Allowing pressure treated wood to dry before installation can yield several advantages:
- Improved Adhesion: If you plan to paint or stain the wood, allowing it to dry ensures better adhesion of finishes.
- Reduced Warp and Twist: Drying helps minimize the natural warping and twisting that can occur in moist wood.
- Better Structural Integrity: Dry wood is less prone to cracking and splitting, which enhances the durability of the installation.
How to Determine if Pressure Treated Wood is Dry
To assess the dryness of pressure treated wood before installation, consider the following methods:
- Moisture Meter: Utilize a moisture meter to measure the moisture content. A reading below 19% generally indicates sufficient dryness for most applications.
- Visual Inspection: Look for signs of moisture, such as discoloration or a damp feel. Wood that feels excessively cool or moist likely still contains high moisture levels.
- Weight Test: Heavier boards may indicate higher moisture content. Lifting and comparing different pieces can provide a rough estimate of their dryness.
Recommended Drying Times
The recommended drying time for pressure treated wood can vary based on environmental conditions. Below is a general guideline:
Condition | Recommended Drying Time |
---|---|
Low Humidity (20-30%) | 1-2 days |
Moderate Humidity (30-50%) | 3-5 days |
High Humidity (50% and above) | 5-7 days or more |
Best Practices for Installation
If you decide to proceed with installation without allowing for extensive drying, consider these best practices:
- Use Proper Fasteners: Select stainless steel or hot-dipped galvanized nails and screws, which resist corrosion better than standard options.
- Leave Gaps: Create small gaps between boards to allow for moisture expansion and contraction.
- Regular Maintenance: Plan for regular inspections and maintenance to address any issues that may arise from moisture retention.
By taking these considerations into account, you can enhance the performance and longevity of your pressure treated wood installations.
Understanding Pressure Treated Wood
Pressure treated wood is commonly used for outdoor projects due to its resistance to decay and insect damage. However, it is essential to consider the moisture content of the wood before installation.
- Moisture Content: Pressure treated wood is often saturated with preservatives and may have a higher moisture content when purchased.
- Drying Process: This wood will need time to acclimate and dry out before being used in certain applications, particularly in enclosed spaces or where dimensional stability is crucial.
Effects of Installing Wet Pressure Treated Wood
Installing pressure treated wood while it is still wet can lead to several issues, including:
- Warping and Splitting: As the wood dries, it may warp or split, compromising the integrity of your structure.
- Fastener Problems: Fasteners may not hold as effectively in wet wood, leading to loosened connections over time.
- Mold and Mildew: Excess moisture can promote mold and mildew growth, affecting the wood’s longevity and safety.
Recommended Drying Times
The recommended drying time for pressure treated wood can vary based on environmental conditions. Below are general guidelines:
Condition | Drying Time |
---|---|
Low humidity (20% or lower) | 1-3 days |
Moderate humidity (20%-50%) | 3-7 days |
High humidity (50% or higher) | 7-14 days |
It’s advisable to check the moisture content with a moisture meter; ideally, it should be below 19% before installation.
Best Practices for Installation
To ensure the longevity and performance of your project, consider the following best practices:
- Acclimatization: Allow the wood to acclimate in the environment where it will be installed for several days.
- Proper Storage: Store pressure treated wood off the ground and in a covered area to prevent direct exposure to moisture.
- Use Appropriate Fasteners: Select corrosion-resistant fasteners to enhance the durability of your installation.
Properly managing the drying process of pressure treated wood before installation is critical. By adhering to recommended practices, you can avoid potential problems, ensuring that your project stands the test of time.
Expert Insights on Drying Pressure Treated Wood Before Installation
Dr. Emily Carter (Wood Science Specialist, Timber Research Institute). “Allowing pressure treated wood to dry before installation is crucial. The drying process reduces moisture content, which helps prevent warping and ensures better adhesion of finishes and sealants applied later.”
Mark Thompson (Construction Project Manager, GreenBuild Solutions). “In my experience, installing pressure treated wood while it is still wet can lead to significant issues down the line, such as shrinkage and cracking. I always recommend letting it dry for at least a few days to achieve optimal performance.”
Lisa Chen (Landscape Architect, EcoDesign Magazine). “When working with pressure treated wood, patience is key. Drying the wood not only enhances its structural integrity but also improves its longevity in outdoor environments, where exposure to moisture is inevitable.”
Frequently Asked Questions (FAQs)
Should I let pressure treated wood dry before installing?
Yes, it is advisable to let pressure treated wood dry for a period before installation. This helps reduce the moisture content, minimizing the risk of warping and ensuring better adhesion for finishes.
How long should I wait for pressure treated wood to dry?
Typically, pressure treated wood should dry for at least 1 to 2 weeks, depending on the climate and humidity levels. In drier conditions, it may dry faster, while humid environments may require a longer drying period.
Can I install pressure treated wood immediately after purchase?
While it is possible to install pressure treated wood immediately, it is not recommended. Installing wet wood can lead to issues such as warping, cracking, and difficulty in applying stains or sealants.
What are the signs that pressure treated wood is dry enough for installation?
Signs that pressure treated wood is dry enough include a lighter color, reduced moisture content, and a lack of surface moisture. A moisture meter can also be used to determine if the wood has reached an appropriate moisture level.
Does drying pressure treated wood affect its longevity?
Yes, allowing pressure treated wood to dry before installation can enhance its longevity. Properly dried wood is less likely to warp or crack, which can compromise its structural integrity over time.
Is it necessary to seal pressure treated wood after it dries?
Sealing pressure treated wood after it dries is highly recommended. A sealant helps protect the wood from moisture, UV rays, and other environmental factors, prolonging its lifespan and maintaining its appearance.
In summary, the decision to let pressure-treated wood dry before installation is influenced by several factors, including the specific type of treatment used, the intended application, and local climate conditions. Pressure-treated wood is often saturated with preservatives, which can lead to warping, cracking, or other structural issues if installed while still wet. Allowing the wood to dry can mitigate these risks, ensuring a more stable and durable installation.
Moreover, the drying process can enhance the adhesion of finishes, stains, or sealants applied post-installation. When pressure-treated wood is installed while still wet, it may not accept these treatments uniformly, potentially leading to an uneven appearance and reduced longevity. Therefore, allowing the wood to acclimate to the environment before installation is a prudent step that can contribute to the overall success of the project.
Ultimately, while it may not be strictly necessary to let pressure-treated wood dry completely before installation, doing so can provide significant benefits. Homeowners and contractors alike should consider local humidity levels and the specific requirements of their project to make an informed decision. Taking the time to properly prepare the wood can lead to better performance and longevity of the finished structure.
Author Profile
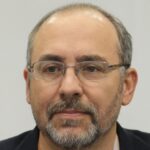
-
Darryl Norman is a seasoned entrepreneur and industry expert with a deep understanding of wood truss manufacturing and construction materials. As the President of Timberlake TrussWorks, LLC, Darryl played a pivotal role in shaping the company’s reputation for quality and precision. His leadership ensured that each truss met rigorous structural standards, providing builders with dependable components essential to their projects.
Beginning in 2025, Darryl Norman has shifted his focus to education and knowledge-sharing through an informative blog dedicated to wood truss manufacturing. Drawing from his extensive experience in the field, he provides in-depth insights into truss design, material selection, and construction techniques. This blog serves as a valuable resource for builders, contractors, and homeowners seeking practical guidance on truss systems and structural integrity.
Latest entries
- March 18, 2025General Wood TopicsWhat Color Is Ebony Wood? Unveiling the Rich Hues of This Luxurious Timber
- March 18, 2025Construction & FrameworkHow Can You Effectively Mount a Headboard to Your Wall?
- March 18, 2025General Wood TopicsCan Bees Really Eat Wood? Unraveling the Myths and Facts
- March 18, 2025General Wood TopicsDo Rabbits Really Chew on Wood? Exploring Their Eating Habits!