What Are the Best Screws for Pressure Treated Wood: A Comprehensive Guide?
When embarking on a woodworking project that involves pressure-treated wood, selecting the right screws is crucial to ensure durability and longevity. Pressure-treated wood is infused with chemicals to resist rot and insects, making it a popular choice for outdoor structures like decks, fences, and furniture. However, not all screws are created equal, and using the wrong type can lead to corrosion, structural failure, and a host of other issues. In this article, we’ll explore the best screws for pressure-treated wood, helping you make informed choices that will enhance the performance and lifespan of your projects.
Understanding the unique properties of pressure-treated wood is essential for any DIY enthusiast or professional builder. The chemicals used in the treatment process can react adversely with certain metals, leading to premature failure of fasteners. Therefore, it’s important to consider factors such as corrosion resistance, strength, and compatibility with the wood itself when selecting screws. In the following sections, we will delve into the various types of screws available, highlighting the materials and coatings that offer the best protection against the elements.
Additionally, we will discuss the importance of screw length and gauge, as these factors play a significant role in achieving a secure and lasting connection. Whether you’re constructing a new deck or repairing an existing structure, understanding the best screws for pressure-treated
Choosing the Right Screws
When selecting screws for pressure-treated wood, it is essential to consider the specific chemical treatments used in the wood, as these can affect the choice of fasteners. The primary concern is corrosion resistance, as pressure-treated wood is often infused with chemicals that can be corrosive to certain metals.
Types of Screws for Pressure-Treated Wood
There are several types of screws that are suitable for use with pressure-treated wood:
- Stainless Steel Screws: These are highly resistant to rust and corrosion, making them ideal for outdoor applications. They are often the best choice for longevity, especially in environments with high moisture.
- Coated Screws: Screws with a special coating, such as epoxy or ceramic, can provide good corrosion resistance. Look for screws specifically labeled for use with pressure-treated wood.
- Galvanized Screws: Hot-dipped galvanized screws offer a reasonable level of corrosion resistance and can be suitable for many outdoor projects. However, they may not be as effective as stainless steel in highly corrosive environments.
- Composite Deck Screws: Designed specifically for composite decking, these screws typically feature a coating that protects against the chemicals in treated wood.
Factors to Consider
When selecting screws for pressure-treated wood, consider the following factors:
- Material Compatibility: Ensure the screw material is compatible with the chemicals in the pressure-treated wood to prevent corrosion.
- Screw Length: The length of the screw should be appropriate for the thickness of the materials being joined.
- Head Type: Different head types (flat, round, or hex) offer various benefits depending on the application and aesthetic preferences.
- Thread Design: Coarse threads provide better grip in softwood, while fine threads are better for hardwood applications.
Screw Type | Corrosion Resistance | Best Applications |
---|---|---|
Stainless Steel | Excellent | Outdoor furniture, decks |
Coated Screws | Good | General construction |
Galvanized | Fair | Decking, fences |
Composite Deck Screws | Good | Composite decking |
Installation Tips
To ensure the best performance of screws in pressure-treated wood, follow these installation tips:
- Pre-drilling: Consider pre-drilling holes to prevent splitting, especially in smaller or thinner boards.
- Screw Placement: Maintain appropriate spacing between screws to allow for wood expansion and contraction.
- Avoid Over-tightening: Over-tightening can lead to damage in the wood and reduce the holding power of the screw.
Best Screws for Pressure Treated Wood
When selecting screws for pressure treated wood, it is essential to consider the specific properties of the wood and the environment in which it will be used. Pressure treated wood is infused with chemicals to resist decay and insect damage, which can affect the choice of fasteners.
Types of Screws
The following types of screws are most suitable for use with pressure treated wood:
- Stainless Steel Screws
- Highly resistant to corrosion and rust.
- Ideal for outdoor applications and coastal areas.
- Galvanized Screws
- Coated with a layer of zinc for corrosion resistance.
- Suitable for moderate exposure to moisture.
- Composite Deck Screws
- Specifically designed for use with composite materials and pressure treated wood.
- Often have a specialized coating to prevent corrosion.
Factors to Consider
Several factors influence the selection of screws for pressure treated wood:
- Corrosion Resistance
- Choose screws with appropriate coatings based on environmental conditions.
- Length and Diameter
- Ensure screws are long enough to penetrate the wood adequately for a secure hold.
- A diameter of 8 to 10 is commonly recommended for most applications.
- Head Type
- Options include flat, pan, or bugle heads, with countersunk heads often preferred for a flush finish.
Recommended Screw Specifications
Screw Type | Coating | Recommended Size | Best For |
---|---|---|---|
Stainless Steel | None | 8 or 10, 2.5″ to 3.5″ | High moisture areas |
Galvanized Screws | Zinc | 8, 2″ to 3″ | General outdoor use |
Composite Deck Screws | Polymer Coating | 8 to 10, 2.5″ to 3.5″ | Decking and composite materials |
Installation Tips
When installing screws in pressure treated wood, consider the following:
- Pre-drill Holes: Prevent splitting, particularly in denser woods, by pre-drilling pilot holes.
- Use the Right Drill Bit: A high-speed steel or carbide-tipped bit is recommended for drilling.
- Maintain Consistent Torque: Avoid over-tightening, which can strip the wood or damage the screw.
Maintenance Considerations
Regular inspections of the screws and the surrounding wood can prevent issues over time:
- Look for signs of corrosion or rust, especially in galvanized screws.
- Check for wood splitting or loosening of screws, which may indicate the need for replacements.
- Reapply protective finishes to the wood to enhance longevity and maintain aesthetics.
Choosing the Right Screws for Pressure Treated Wood
Laura Thompson (Woodworking Specialist, TimberTech Solutions). “When selecting screws for pressure treated wood, it is crucial to opt for stainless steel or coated screws. These materials resist corrosion and ensure longevity, especially in outdoor environments where moisture is a concern.”
Michael Chen (Construction Materials Engineer, BuildSmart Innovations). “I recommend using screws that are specifically labeled as ‘decking screws’ for pressure treated wood. These screws are designed with a sharp point and a thread that enhances grip, preventing splitting and ensuring a secure hold.”
Jessica Ramirez (Landscape Architect, GreenScape Designs). “For projects involving pressure treated wood, it’s essential to consider the length and gauge of the screws. A minimum of 2.5 inches in length is advisable for structural integrity, while a thicker gauge will provide added strength, especially in high-stress applications.”
Frequently Asked Questions (FAQs)
What are the best screws for pressure treated wood?
The best screws for pressure treated wood are typically stainless steel, galvanized, or coated screws specifically designed for outdoor use. These materials resist corrosion and degradation caused by moisture and chemicals in treated wood.
Why should I use stainless steel screws for pressure treated wood?
Stainless steel screws offer superior resistance to rust and corrosion, making them ideal for environments with high moisture levels, such as decks or outdoor structures made from pressure treated wood.
Can I use regular screws for pressure treated wood?
Regular screws may not withstand the harsh conditions associated with pressure treated wood. They are prone to rust and corrosion, which can lead to structural failure over time.
What size screws should I use for pressure treated wood?
The size of screws depends on the specific application, but generally, 2.5 to 3-inch screws are recommended for fastening boards together. Always ensure the screw penetrates at least 1.5 inches into the underlying material for optimal holding strength.
Are there specific brands known for quality screws for pressure treated wood?
Brands such as Deck Mate, Simpson Strong-Tie, and GRK Fasteners are well-regarded for producing high-quality screws suitable for pressure treated wood applications.
How can I prevent wood splitting when using screws in pressure treated wood?
To prevent wood splitting, pre-drill pilot holes slightly smaller than the screw diameter. This reduces stress on the wood fibers and allows for easier insertion of the screws.
selecting the best screws for pressure-treated wood is crucial for ensuring the longevity and stability of your projects. Due to the chemicals used in the treatment process, it is essential to choose screws that can withstand corrosion. Stainless steel screws, particularly those made of 316-grade stainless steel, are often recommended for their superior resistance to rust and degradation. Additionally, coated screws, such as those with a polymer or epoxy finish, provide a cost-effective alternative while still offering adequate protection against the elements.
Another important factor to consider is the screw type and design. Deck screws, which typically feature a sharp point and aggressive thread design, are ideal for securing pressure-treated wood. They are specifically engineered to drive easily into dense materials and provide a strong hold. Furthermore, using screws with a larger diameter can enhance the structural integrity of the connection, especially in load-bearing applications.
Lastly, proper installation techniques should not be overlooked. Pre-drilling pilot holes can help prevent splitting in the wood, particularly in denser areas. Additionally, following the manufacturer’s guidelines for spacing and depth will further ensure the durability of the construction. By paying attention to these details, you can achieve a robust and lasting result when working with pressure-treated wood.
Author Profile
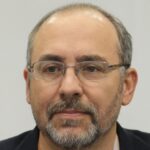
-
Darryl Norman is a seasoned entrepreneur and industry expert with a deep understanding of wood truss manufacturing and construction materials. As the President of Timberlake TrussWorks, LLC, Darryl played a pivotal role in shaping the company’s reputation for quality and precision. His leadership ensured that each truss met rigorous structural standards, providing builders with dependable components essential to their projects.
Beginning in 2025, Darryl Norman has shifted his focus to education and knowledge-sharing through an informative blog dedicated to wood truss manufacturing. Drawing from his extensive experience in the field, he provides in-depth insights into truss design, material selection, and construction techniques. This blog serves as a valuable resource for builders, contractors, and homeowners seeking practical guidance on truss systems and structural integrity.
Latest entries
- March 18, 2025General Wood TopicsWhat Color Is Ebony Wood? Unveiling the Rich Hues of This Luxurious Timber
- March 18, 2025Construction & FrameworkHow Can You Effectively Mount a Headboard to Your Wall?
- March 18, 2025General Wood TopicsCan Bees Really Eat Wood? Unraveling the Myths and Facts
- March 18, 2025General Wood TopicsDo Rabbits Really Chew on Wood? Exploring Their Eating Habits!