What Is Compressed Wood and How Is It Made?
What Is Compressed Wood?
In a world increasingly focused on sustainability and innovative materials, compressed wood has emerged as a fascinating solution that marries functionality with eco-friendliness. This unique material, often referred to as engineered wood, is transforming the way we think about construction, furniture design, and everyday products. By utilizing wood fibers that are compacted under high pressure, compressed wood not only maximizes the use of natural resources but also enhances the durability and versatility of wood-based products. As we delve into the intricacies of compressed wood, we’ll uncover its benefits, applications, and the technology behind its creation, revealing why it’s becoming a go-to choice for architects, designers, and environmentally conscious consumers alike.
Compressed wood is produced through a process that involves binding wood fibers together, resulting in a denser and stronger material compared to traditional wood. This method not only reduces waste by utilizing smaller wood particles but also allows for the creation of products that can withstand greater stress and wear. The applications of compressed wood are vast, ranging from furniture and flooring to construction materials, making it a highly sought-after option in various industries.
Moreover, the environmental impact of compressed wood is a significant factor in its growing popularity. By promoting the use of renewable resources and reducing the need for
Composition of Compressed Wood
Compressed wood is primarily made from wood fibers, which are derived from various tree species. These fibers undergo a process of compression that significantly alters their structure and properties. The main components involved in the production of compressed wood include:
- Wood Fibers: Sourced from softwood or hardwood trees, these fibers are the fundamental building blocks of compressed wood.
- Adhesives: Synthetic or natural adhesives are often used to bind the wood fibers together during the compression process.
- Additives: Various additives may be included to enhance properties such as fire resistance, moisture resistance, and durability.
The combination of these materials allows for the creation of a dense, strong composite that is suitable for a wide range of applications.
Manufacturing Process
The manufacturing process of compressed wood involves several critical steps that ensure the final product meets desired specifications. The typical process includes:
- Raw Material Preparation: Wood is processed into fibers, either through mechanical means or chemical treatment.
- Mixing: The wood fibers are mixed with adhesives and any necessary additives to form a homogeneous material.
- Compression: The mixture is subjected to high pressure and temperature, which compresses the fibers and activates the adhesives, forming a solid mass.
- Cooling and Curing: After compression, the material is cooled and cured to ensure the adhesives bond effectively and the structure stabilizes.
- Finishing: The compressed wood is then cut, sanded, and finished to meet the required dimensions and surface quality.
Properties of Compressed Wood
Compressed wood exhibits a variety of properties that make it suitable for diverse applications. Some of the notable characteristics include:
- High Strength-to-Weight Ratio: Compressed wood is lightweight yet strong, making it ideal for use in furniture and construction.
- Dimensional Stability: The compression process reduces the wood’s tendency to warp or shrink, providing greater stability over time.
- Moisture Resistance: Depending on the additives used, compressed wood can resist moisture, preventing deterioration in humid environments.
- Sustainability: Utilizing recycled wood fibers contributes to environmental sustainability by reducing waste and conserving resources.
Property | Description |
---|---|
Density | Higher density compared to traditional wood, leading to improved strength. |
Fire Resistance | Can be treated to enhance fire resistance, making it safer for various applications. |
Versatility | Used in furniture, flooring, and construction materials due to its adaptability. |
Applications of Compressed Wood
Compressed wood is utilized across multiple industries due to its advantageous properties. Common applications include:
- Furniture Manufacturing: Used in tabletops, cabinets, and chairs for its strength and aesthetic appeal.
- Flooring: Provides a durable surface that can withstand heavy foot traffic.
- Construction: Employed in structural components such as beams and panels.
- Packaging: Offers a sturdy option for shipping and storage solutions.
The versatility and resilience of compressed wood continue to drive innovation in its applications, making it a popular choice for manufacturers and consumers alike.
Definition of Compressed Wood
Compressed wood, often referred to as engineered wood or wood composites, is a material created by binding together wood fibers, particles, or veneers under heat and pressure. This process enhances the physical properties of the wood, making it more durable and versatile for various applications.
Manufacturing Process
The manufacturing of compressed wood involves several key steps:
- Material Selection: Choosing suitable wood species or by-products, such as sawdust or wood chips.
- Preparation: The raw materials are cleaned and processed into smaller particles or fibers.
- Mixing: The wood particles are mixed with adhesives and other additives to enhance durability and resistance to moisture.
- Forming: The mixture is placed into molds and subjected to high pressure and temperature, which compresses the wood fibers together.
- Curing: The formed panels or products are cured to ensure the adhesives bond properly and the material gains strength.
Types of Compressed Wood
Compressed wood comes in various forms, each designed for specific uses:
- Plywood: Made from layers of veneer glued together, offering strength and stability.
- Particle Board: Composed of wood chips and resin, commonly used in furniture and cabinetry.
- Medium Density Fiberboard (MDF): Made from wood fibers that are compressed into dense sheets, ideal for decorative applications.
- Oriented Strand Board (OSB): Constructed from strands of wood arranged in specific orientations, providing structural integrity.
Properties of Compressed Wood
Compressed wood exhibits several beneficial properties:
Property | Description |
---|---|
Strength | Higher load-bearing capacity compared to solid wood. |
Uniformity | Consistent density and thickness across the surface. |
Moisture Resistance | Enhanced resistance to warping and swelling. |
Versatility | Suitable for a wide range of applications, from furniture to construction. |
Applications of Compressed Wood
The diverse applications of compressed wood include:
- Furniture: Used in tables, chairs, and cabinetry due to its aesthetics and affordability.
- Construction: Employed in flooring, wall panels, and roofing materials, offering structural support.
- Interior Design: Ideal for decorative panels and moldings due to its ability to be easily shaped and finished.
- Transport: Utilized in pallets and crates for shipping due to its lightweight and strong nature.
Environmental Considerations
Compressed wood is often viewed as an environmentally friendly option, particularly when derived from sustainable sources. Key considerations include:
- Recycling: Many products are made from recycled wood materials, reducing waste.
- Sustainability: The use of fast-growing tree species can minimize environmental impact.
- Low Emission Options: Advances in adhesive technology have led to lower volatile organic compound (VOC) emissions, making compressed wood a safer choice for indoor applications.
Understanding compressed wood and its properties allows for informed decisions in material selection, ensuring the suitability for various applications while considering environmental impacts.
Understanding Compressed Wood: Perspectives from Experts
Dr. Emily Carter (Materials Scientist, Wood Technology Institute). “Compressed wood, often referred to as engineered wood, is a product created by applying heat and pressure to wood fibers. This process enhances its density and strength, making it a sustainable alternative to traditional lumber in various applications, from furniture to construction.”
James Thompson (Sustainability Consultant, Green Building Council). “The use of compressed wood is pivotal in the movement towards sustainable building practices. By utilizing wood waste and reducing the need for virgin timber, compressed wood products not only lower environmental impact but also contribute to energy efficiency in buildings.”
Linda Martinez (Interior Designer, EcoDesign Studio). “In interior design, compressed wood offers both aesthetic and functional benefits. Its versatility allows for innovative designs while providing durability and resistance to warping, making it an ideal choice for modern spaces.”
Frequently Asked Questions (FAQs)
What is compressed wood?
Compressed wood is a type of engineered wood product created by compressing wood fibers or particles under high pressure and heat. This process enhances its density and strength, making it suitable for various applications.
What are the main uses of compressed wood?
Compressed wood is commonly used in furniture manufacturing, flooring, cabinetry, and construction materials. Its durability and aesthetic appeal make it a popular choice in both residential and commercial settings.
How is compressed wood different from solid wood?
Unlike solid wood, which is cut from trees, compressed wood is manufactured from wood particles or fibers. This process allows for more efficient use of wood resources and can result in a more uniform product with fewer defects.
Is compressed wood environmentally friendly?
Compressed wood can be environmentally friendly, especially when sourced from sustainably managed forests. Additionally, it often utilizes wood waste and by-products, reducing overall waste in the industry.
What are the advantages of using compressed wood?
The advantages of compressed wood include its cost-effectiveness, resistance to warping and splitting, and versatility in design. It also offers a consistent appearance and can be produced in various finishes.
Are there any disadvantages to compressed wood?
While compressed wood is durable, it can be less resistant to moisture compared to solid wood. Additionally, some types may emit formaldehyde and other volatile organic compounds (VOCs), so selecting low-emission products is advisable.
Compressed wood, also known as engineered wood, is a material created by binding together wood fibers, particles, or veneers under heat and pressure. This process enhances the wood’s density and strength, making it suitable for various applications, including furniture, flooring, and construction. The primary advantage of compressed wood is its ability to utilize lower-quality wood resources, reducing waste and promoting sustainability in the timber industry.
The manufacturing process of compressed wood involves several steps, including drying the raw materials, applying adhesives, and then compressing the mixture in a mold. The result is a product that can be tailored to specific needs, offering versatility in design and functionality. Compressed wood products, such as particleboard and plywood, are often more affordable than solid wood, making them accessible for a broader range of consumers.
Additionally, compressed wood exhibits properties such as resistance to warping and cracking, which are common issues with solid wood. However, it is essential to note that some compressed wood products may contain formaldehyde-based adhesives, raising concerns about indoor air quality. Therefore, consumers should look for low-emission options when selecting compressed wood products.
compressed wood represents an innovative solution within the woodworking industry, combining sustainability with practicality.
Author Profile
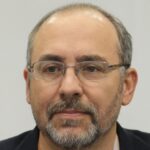
-
Darryl Norman is a seasoned entrepreneur and industry expert with a deep understanding of wood truss manufacturing and construction materials. As the President of Timberlake TrussWorks, LLC, Darryl played a pivotal role in shaping the company’s reputation for quality and precision. His leadership ensured that each truss met rigorous structural standards, providing builders with dependable components essential to their projects.
Beginning in 2025, Darryl Norman has shifted his focus to education and knowledge-sharing through an informative blog dedicated to wood truss manufacturing. Drawing from his extensive experience in the field, he provides in-depth insights into truss design, material selection, and construction techniques. This blog serves as a valuable resource for builders, contractors, and homeowners seeking practical guidance on truss systems and structural integrity.
Latest entries
- March 18, 2025General Wood TopicsWhat Color Is Ebony Wood? Unveiling the Rich Hues of This Luxurious Timber
- March 18, 2025Construction & FrameworkHow Can You Effectively Mount a Headboard to Your Wall?
- March 18, 2025General Wood TopicsCan Bees Really Eat Wood? Unraveling the Myths and Facts
- March 18, 2025General Wood TopicsDo Rabbits Really Chew on Wood? Exploring Their Eating Habits!