What Is Pressed Wood and How Is It Made?
What Is Pressed Wood?
In the world of furniture and construction, pressed wood has carved out a significant niche, becoming a staple material for countless applications. From the sleek cabinets in our kitchens to the sturdy desks in our offices, pressed wood offers a blend of affordability, versatility, and aesthetic appeal that has made it a popular choice among manufacturers and consumers alike. But what exactly is pressed wood, and how does it differ from traditional solid wood? This article delves into the intricacies of pressed wood, exploring its composition, manufacturing processes, and the advantages and disadvantages it presents in various contexts.
Pressed wood, often referred to as engineered wood or composite wood, is created by binding together wood fibers, particles, or veneers using adhesives and heat. This innovative approach not only maximizes the use of wood resources but also allows for the creation of materials that can be tailored to specific needs. The resulting products, such as particleboard, MDF (medium-density fiberboard), and plywood, exhibit unique properties that make them suitable for a wide range of applications, from furniture production to construction.
As we navigate through the characteristics and uses of pressed wood, we will also touch on its environmental impact, durability, and maintenance considerations. Understanding these factors will empower you to make informed decisions when
Composition of Pressed Wood
Pressed wood, also known as engineered wood, is made by binding together wood fibers, particles, or veneers using adhesives under heat and pressure. This process results in a durable and versatile material that mimics the appearance of solid wood while providing several additional benefits. The primary components of pressed wood include:
- Wood Fibers: These can be derived from various sources, including sawmill waste, wood shavings, and reclaimed wood.
- Adhesives: Used to bond the wood particles, the type and quality of adhesive significantly affect the strength and durability of the final product.
- Additives: Chemicals may be included to enhance properties such as moisture resistance, fire resistance, and pest control.
Different types of pressed wood products are created based on the size and type of wood particles used, as well as the manufacturing process.
Types of Pressed Wood
Pressed wood can be categorized into several types, each with distinct characteristics and applications:
- Particleboard: Made from small wood particles and adhesive, particleboard is commonly used for furniture and cabinetry.
- Medium Density Fiberboard (MDF): Composed of finely ground wood fibers, MDF offers a smooth surface ideal for painting and veneering, making it a popular choice for decorative applications.
- Oriented Strand Board (OSB): Made from strands of wood arranged in specific orientations, OSB is primarily used in construction for sheathing and flooring.
- Plywood: Created from layers of wood veneers glued together, plywood is strong and versatile, suitable for structural and decorative uses.
Type | Composition | Common Uses |
---|---|---|
Particleboard | Wood particles and adhesive | Furniture, cabinetry |
MDF | Wood fibers and adhesive | Decorative applications, cabinetry |
OSB | Wood strands in layers | Construction sheathing, flooring |
Plywood | Wood veneers | Structural uses, furniture |
Advantages of Pressed Wood
Pressed wood offers several advantages over traditional solid wood, including:
- Cost-Effectiveness: Pressed wood is generally less expensive to produce, making it an economical choice for consumers.
- Sustainability: The use of recycled wood materials and by-products contributes to more sustainable manufacturing practices.
- Uniformity: Pressed wood products provide consistent quality and size, reducing the likelihood of warping or splitting.
- Versatility: Available in various forms and finishes, pressed wood can be tailored for a wide range of applications.
Environmental Considerations
While pressed wood presents various benefits, environmental concerns also arise due to the adhesives used in production, which can emit volatile organic compounds (VOCs). It is essential to select products that meet eco-friendly standards, such as:
- Low-VOC Emissions: Choosing pressed wood certified for low emissions can minimize indoor air pollution.
- Recycled Content: Products containing recycled wood contribute to resource conservation.
Understanding these aspects can aid consumers in making informed choices regarding pressed wood products.
Definition of Pressed Wood
Pressed wood, also known as engineered wood or composite wood, refers to a variety of wood products made by binding together strands, fibers, or veneers of wood with adhesives to form a composite material. This process enhances the physical properties of the wood, making it more durable and versatile for various applications. Common types of pressed wood include particle board, medium-density fiberboard (MDF), and oriented strand board (OSB).
Manufacturing Process
The manufacturing of pressed wood involves several key steps:
- Raw Material Preparation: Wood chips, fibers, or veneers are gathered and processed.
- Drying: The raw materials are dried to reduce moisture content, which is crucial for adhesion.
- Mixing: Adhesives are mixed with the wood materials to ensure a strong bond.
- Forming: The mixture is placed into molds or sheets and subjected to heat and pressure to shape it.
- Curing: The pressed wood is cured to allow the adhesives to set and bond the materials together.
- Finishing: The final product may be sanded, cut, or coated for aesthetic and functional purposes.
Types of Pressed Wood
Pressed wood products come in several types, each with distinct characteristics:
Type | Composition | Common Uses |
---|---|---|
Particle Board | Wood particles bonded with adhesive | Furniture, cabinetry, and shelving |
Medium-Density Fiberboard (MDF) | Wood fibers compressed and bonded | Cabinet doors, moldings, and panels |
Oriented Strand Board (OSB) | Wood strands arranged in layers | Sheathing, flooring, and roof decking |
Plywood | Layers of wood veneers glued together | Structural applications, furniture |
Advantages of Pressed Wood
Pressed wood offers several advantages, including:
- Cost-Effectiveness: Generally more affordable than solid wood.
- Sustainability: Utilizes wood byproducts, reducing waste.
- Versatility: Available in various thicknesses and sizes for different applications.
- Stability: Less prone to warping and cracking compared to solid wood.
- Uniformity: Provides a consistent surface and density, facilitating machining and finishing.
Disadvantages of Pressed Wood
Despite its advantages, pressed wood has some drawbacks:
- Durability: May not be as strong as solid wood; susceptible to damage from moisture.
- Chemical Emissions: Some products may release volatile organic compounds (VOCs) from adhesives.
- Limited Aesthetic Appeal: Generally lacks the natural beauty and grain patterns of solid wood.
Applications of Pressed Wood
Pressed wood is widely used in various industries, including:
- Furniture Manufacturing: For making cabinets, tables, and chairs.
- Construction: Used as sheathing, flooring, and roofing materials.
- Interior Design: Employed in wall panels, moldings, and decorative elements.
Maintenance and Care
Proper maintenance of pressed wood products can prolong their lifespan:
- Avoid Excess Moisture: Keep away from water exposure to prevent swelling and damage.
- Regular Cleaning: Use a damp cloth to clean surfaces, avoiding harsh chemicals.
- Temperature Control: Maintain consistent indoor temperatures to reduce expansion and contraction.
Understanding Pressed Wood: Expert Perspectives
Dr. Emily Carter (Materials Scientist, Wood Technology Institute). “Pressed wood, often referred to as engineered wood, is created by compressing wood fibers or particles with adhesives under heat and pressure. This process enhances the material’s strength and durability, making it a popular choice for furniture and construction.”
Mark Thompson (Furniture Design Expert, Home Decor Magazine). “The versatility of pressed wood allows designers to create a wide range of products while maintaining cost-effectiveness. Its ability to mimic the appearance of solid wood without the associated price tag makes it an attractive option for both manufacturers and consumers.”
Linda Garcia (Sustainability Consultant, Green Building Council). “While pressed wood products can be more environmentally friendly than traditional lumber, it is crucial to consider the types of adhesives used. Choosing low-VOC or formaldehyde-free options can significantly reduce the environmental impact of these materials.”
Frequently Asked Questions (FAQs)
What is pressed wood?
Pressed wood, also known as engineered wood or composite wood, is a manufactured product created by binding together wood fibers, strands, or veneers with adhesives under heat and pressure. This process results in a dense, durable material used in various applications, including furniture and construction.
What are the types of pressed wood?
The main types of pressed wood include particleboard, medium-density fiberboard (MDF), and plywood. Each type has distinct characteristics and uses, with particleboard being composed of small wood particles, MDF made from fine wood fibers, and plywood consisting of layers of veneer glued together.
What are the advantages of using pressed wood?
Pressed wood offers several advantages, including cost-effectiveness, versatility in design, and ease of manufacturing. It can be produced in various sizes and shapes, making it suitable for a wide range of applications, from furniture to cabinetry.
Are there any environmental concerns associated with pressed wood?
Yes, there are environmental concerns related to pressed wood, primarily due to the adhesives used in the manufacturing process, which may contain formaldehyde and other volatile organic compounds (VOCs). However, many manufacturers now produce low-emission or formaldehyde-free options to mitigate these concerns.
How does pressed wood compare to solid wood?
Pressed wood typically costs less than solid wood and is more uniform in appearance and size. However, solid wood is generally stronger, more durable, and can be refinished multiple times, while pressed wood may be more susceptible to moisture damage and cannot be sanded or refinished effectively.
Is pressed wood safe for indoor use?
Pressed wood can be safe for indoor use, provided it meets safety standards regarding emissions. It is advisable to choose products labeled as low-VOC or formaldehyde-free to ensure a healthier indoor environment.
Pressed wood, also known as engineered wood or composite wood, is a material created by binding together wood fibers, particles, or veneers using adhesives and heat. This process results in products such as particleboard, medium-density fiberboard (MDF), and plywood, which are widely used in furniture, cabinetry, and construction. The manufacturing of pressed wood allows for efficient use of wood resources, as it can incorporate smaller or less desirable wood pieces that might otherwise go to waste.
One of the key advantages of pressed wood is its versatility and cost-effectiveness. It can be produced in various thicknesses and finishes, making it suitable for a range of applications. Additionally, pressed wood products can be engineered to have specific properties, such as moisture resistance or enhanced strength, which broadens their usability in different environments. However, it is important to consider the environmental impact and health concerns associated with the adhesives used in some pressed wood products, particularly those that may emit volatile organic compounds (VOCs).
pressed wood represents a significant advancement in wood product technology, offering sustainable alternatives to solid wood while meeting diverse consumer needs. Understanding the characteristics and applications of pressed wood can help consumers make informed choices regarding their use in various projects. As the demand
Author Profile
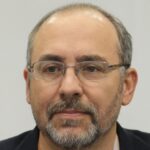
-
Darryl Norman is a seasoned entrepreneur and industry expert with a deep understanding of wood truss manufacturing and construction materials. As the President of Timberlake TrussWorks, LLC, Darryl played a pivotal role in shaping the company’s reputation for quality and precision. His leadership ensured that each truss met rigorous structural standards, providing builders with dependable components essential to their projects.
Beginning in 2025, Darryl Norman has shifted his focus to education and knowledge-sharing through an informative blog dedicated to wood truss manufacturing. Drawing from his extensive experience in the field, he provides in-depth insights into truss design, material selection, and construction techniques. This blog serves as a valuable resource for builders, contractors, and homeowners seeking practical guidance on truss systems and structural integrity.
Latest entries
- March 18, 2025General Wood TopicsWhat Color Is Ebony Wood? Unveiling the Rich Hues of This Luxurious Timber
- March 18, 2025Construction & FrameworkHow Can You Effectively Mount a Headboard to Your Wall?
- March 18, 2025General Wood TopicsCan Bees Really Eat Wood? Unraveling the Myths and Facts
- March 18, 2025General Wood TopicsDo Rabbits Really Chew on Wood? Exploring Their Eating Habits!