What Is Wood Checking and How Does It Affect Your Woodworking Projects?
Wood checking is a phenomenon that intrigues both woodworking enthusiasts and professionals alike, as it reveals the complex relationship between wood and its environment. As timber dries and ages, it can develop cracks and splits, known as checks, which can affect both the aesthetic and structural integrity of the material. Understanding wood checking is essential for anyone involved in woodworking, construction, or furniture making, as it not only impacts the quality of the finished product but also informs best practices for wood selection and treatment.
At its core, wood checking is a natural process that occurs as moisture evaporates from the wood fibers. This drying process can lead to uneven shrinkage, causing the surface of the wood to crack. Various factors contribute to the severity and appearance of checks, including the type of wood, the drying conditions, and the initial moisture content. While some may view checking as a flaw, others appreciate the unique character it adds to wood products, particularly in rustic or reclaimed designs.
In the following sections, we will delve deeper into the causes and implications of wood checking, exploring how it can be managed or even embraced in woodworking projects. Whether you are a seasoned craftsman or a curious novice, understanding this natural occurrence will enhance your appreciation of wood and its many possibilities.
Understanding Wood Checking
Wood checking refers to the formation of cracks or splits in the surface of wood as it dries. This phenomenon can occur in various types of wood and is influenced by several factors, including the species of wood, its moisture content, and the environmental conditions during the drying process.
The primary cause of wood checking is the uneven drying of the wood fibers. As wood loses moisture, it shrinks. If the surface of the wood dries faster than the interior, tension builds up, leading to cracks. These checks can occur on the ends of the wood, known as end checks, or along the sides, referred to as surface checks.
Factors Influencing Wood Checking
Several factors contribute to the occurrence of wood checking:
- Moisture Content: Higher moisture content increases the likelihood of checking, particularly if the wood is dried too quickly.
- Wood Species: Some species are more prone to checking due to their cellular structure. For instance, oak and cherry are known to check more readily than denser woods like maple.
- Drying Method: Air drying versus kiln drying can lead to different checking patterns. Kiln drying, if not properly managed, can exacerbate the issue.
- Environmental Conditions: Temperature and humidity levels during drying play a crucial role. Rapid changes in these conditions can lead to checking.
Types of Wood Checks
Wood checks can be categorized based on their location and severity:
- End Checks: Cracks that occur at the ends of the wood, often due to rapid moisture loss.
- Surface Checks: Cracks that form along the grain on the surface of the wood.
- Through Checks: Deep cracks that extend completely through the wood, potentially affecting structural integrity.
Preventing Wood Checking
Preventing wood checking is essential for maintaining the quality of wood products. Effective strategies include:
- Controlled Drying: Gradually drying wood in a controlled environment to minimize moisture loss.
- Sealing Ends: Applying sealants to the ends of cut lumber to reduce moisture evaporation.
- Consistent Humidity: Keeping the drying environment stable in terms of humidity and temperature.
- Proper Stacking: Stacking wood with spacers to allow air circulation can promote even drying.
Impact of Wood Checking on Quality
Checking can significantly affect the appearance and usability of wood. In many cases, severe checks can render wood unsuitable for high-quality applications such as furniture making. However, some woodworkers embrace checks for aesthetic reasons, as they can add character to the final product.
Type of Check | Common Causes | Impact on Wood |
---|---|---|
End Check | Rapid moisture loss at ends | Can lead to structural weakness |
Surface Check | Uneven drying | Affects finish and appearance |
Through Check | Extreme drying conditions | May compromise integrity |
Understanding Wood Checking
Wood checking refers to the formation of cracks or splits in wood, often occurring during the drying process. These checks can impact both the structural integrity and aesthetic appeal of wood products. Understanding the causes and implications of wood checking is essential for woodworkers, builders, and manufacturers.
Causes of Wood Checking
Several factors contribute to the occurrence of wood checking:
- Moisture Content: Rapid loss of moisture from the wood can lead to uneven shrinkage, causing stress and cracks.
- Temperature Changes: Fluctuations in temperature can affect the rate of drying and lead to checking.
- Wood Species: Different species have varying susceptibility to checking due to their density and cell structure.
- Wood Thickness: Thicker pieces of wood are more prone to checking as moisture escapes from the surface.
- Drying Method: Air drying versus kiln drying can yield different results, with kiln drying often leading to more controlled moisture loss.
Types of Checks
Wood checking can manifest in various forms, each with distinct characteristics:
Type of Check | Description |
---|---|
Surface Checks | Shallow cracks that appear on the surface. |
Internal Checks | Deeper fractures that may not be visible externally. |
End Checks | Cracks that occur at the ends of the wood, often due to moisture loss. |
Radial Checks | Cracks that extend from the center of the wood outward. |
Effects of Wood Checking
The presence of checks can lead to several negative outcomes:
- Structural Weakness: Checks can compromise the load-bearing capacity of the wood.
- Aesthetic Issues: Visible cracks may detract from the appearance of finished products.
- Increased Risk of Decay: Cracks can provide entry points for moisture and pests, leading to further degradation.
- Reduced Value: Wood with significant checking may be less desirable in the market.
Preventing Wood Checking
To minimize the risk of wood checking, consider the following strategies:
- Controlled Drying: Utilize slow and controlled drying methods to reduce stress on the wood.
- Moisture Monitoring: Regularly check moisture levels to ensure balanced drying.
- Sealants: Apply sealants to the ends of cut timber to slow moisture loss.
- Proper Storage: Store wood in a stable environment, protected from extreme temperatures and humidity changes.
Treatment of Checked Wood
When dealing with checked wood, several treatment options are available:
- Filling: Use epoxy or wood filler to repair surface checks for aesthetic purposes.
- Stabilization: Consider reinforcing checked wood with brackets or other support structures.
- Reconditioning: Rehydrate the wood carefully to reduce the severity of the checks, followed by controlled drying.
By understanding the nature of wood checking and employing effective prevention and treatment methods, individuals and professionals can better manage wood quality and longevity.
Understanding Wood Checking: Insights from Experts
Dr. Emily Carter (Wood Science Researcher, Timber Innovations Institute). “Wood checking, often referred to as cracking or splitting, occurs when wood dries unevenly. This phenomenon can significantly affect the structural integrity and aesthetic quality of timber products, making it essential for manufacturers to implement proper drying techniques.”
James Thompson (Master Carpenter, Artisan Woodworks). “In my experience, wood checking is a common issue that can arise from rapid temperature changes or high humidity levels. Understanding the environmental factors that contribute to checking is crucial for anyone working with wood, as it can lead to costly repairs or replacements.”
Linda Martinez (Sustainable Forestry Consultant, EcoWood Solutions). “Preventing wood checking starts in the forest. Proper harvesting and storage practices can minimize moisture loss and help maintain the wood’s integrity. Education on these practices is vital for both producers and consumers to ensure sustainable use of wood resources.”
Frequently Asked Questions (FAQs)
What is wood checking?
Wood checking refers to the formation of cracks or splits in the wood surface due to the drying process. These checks typically occur as the wood shrinks and can affect both the aesthetic and structural integrity of the material.
What causes wood checking?
Wood checking is primarily caused by uneven drying or rapid moisture loss. Factors such as environmental conditions, wood species, and the initial moisture content significantly influence the likelihood of checking.
Is wood checking harmful to furniture?
While wood checking can detract from the visual appeal of furniture, it does not always compromise structural strength. However, extensive checks can lead to further degradation if moisture enters and causes additional damage.
Can wood checking be prevented?
Preventative measures include proper drying techniques, maintaining consistent humidity levels, and using sealants or finishes that minimize moisture loss. Selecting the right wood species for specific applications can also reduce the risk of checking.
How can I repair wood checking?
Repairing wood checking can involve filling the cracks with wood filler or epoxy, sanding the area smooth, and applying a finish to match the surrounding wood. For significant checks, professional restoration may be advisable.
Does wood checking affect the value of lumber?
Yes, wood checking can negatively impact the value of lumber, especially if it affects the wood’s appearance or structural properties. Buyers often prefer wood with minimal defects, which can lead to lower market prices for checked wood.
Wood checking refers to the formation of cracks or splits in the surface of wood, typically occurring as a result of uneven drying or changes in moisture content. This phenomenon can significantly affect the aesthetic and structural integrity of wooden materials, making it an important consideration for woodworkers, builders, and manufacturers. Understanding the causes and implications of wood checking is essential for anyone involved in the use or treatment of wood products.
The primary causes of wood checking include rapid drying, fluctuations in humidity, and the inherent properties of the wood species. When wood dries too quickly, the outer layers may lose moisture faster than the inner layers, leading to stress and eventual cracking. Additionally, environmental factors such as temperature and humidity can exacerbate the issue, making it crucial to monitor and control these conditions during the drying process.
To mitigate wood checking, several preventative measures can be implemented. These include proper kiln drying techniques, using sealants to slow moisture loss, and selecting appropriate wood species that are less prone to checking. By understanding and addressing the factors that contribute to wood checking, stakeholders can enhance the longevity and performance of wood products, ensuring their quality and usability in various applications.
Author Profile
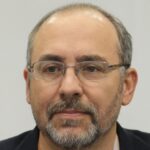
-
Darryl Norman is a seasoned entrepreneur and industry expert with a deep understanding of wood truss manufacturing and construction materials. As the President of Timberlake TrussWorks, LLC, Darryl played a pivotal role in shaping the company’s reputation for quality and precision. His leadership ensured that each truss met rigorous structural standards, providing builders with dependable components essential to their projects.
Beginning in 2025, Darryl Norman has shifted his focus to education and knowledge-sharing through an informative blog dedicated to wood truss manufacturing. Drawing from his extensive experience in the field, he provides in-depth insights into truss design, material selection, and construction techniques. This blog serves as a valuable resource for builders, contractors, and homeowners seeking practical guidance on truss systems and structural integrity.
Latest entries
- March 18, 2025General Wood TopicsWhat Color Is Ebony Wood? Unveiling the Rich Hues of This Luxurious Timber
- March 18, 2025Construction & FrameworkHow Can You Effectively Mount a Headboard to Your Wall?
- March 18, 2025General Wood TopicsCan Bees Really Eat Wood? Unraveling the Myths and Facts
- March 18, 2025General Wood TopicsDo Rabbits Really Chew on Wood? Exploring Their Eating Habits!