What Kind of Wood Is Used for Xylophones: What You Need to Know?
The xylophone, a beloved percussion instrument known for its bright, melodic tones, has captivated audiences around the world for centuries. But have you ever stopped to wonder what gives this instrument its distinctive sound? The answer lies in the type of wood used to craft the bars of the xylophone. The choice of wood not only influences the instrument’s tonal quality but also its durability and overall aesthetic appeal. In this article, we will explore the various types of wood commonly used in xylophone construction, delving into their unique characteristics and how they contribute to the music we enjoy.
When it comes to xylophone bars, the selection of wood is crucial. Different woods offer varying densities and resonant qualities, which can dramatically affect the sound produced. For instance, hardwoods are often preferred for their ability to produce clear, sustained tones, while softer woods may lend a warmer, mellower sound. This interplay between wood type and sound quality is a fascinating aspect of instrument making that musicians and enthusiasts alike should appreciate.
In addition to tonal properties, the choice of wood also impacts the xylophone’s appearance and longevity. Some woods are more resistant to environmental changes, ensuring that the instrument remains in tune and visually appealing over time. As we delve deeper into
Types of Wood Used in Xylophones
Xylophones are percussion instruments made from wooden bars that produce musical tones when struck. The choice of wood is crucial for the instrument’s sound quality, durability, and aesthetic appeal. Several types of wood are commonly used in the construction of xylophones:
- Rosewood: Historically, rosewood has been the preferred wood for high-quality xylophones due to its dense structure and rich tonal qualities. It produces a warm, resonant sound that is highly valued in orchestral and solo performances.
- Padauk: This wood is often used as a substitute for rosewood. It offers a bright, clear tone and is more sustainable. Padauk is lighter than rosewood, which can affect the overall weight and resonance of the instrument.
- Birch: Birch is a more economical choice and is frequently used for student models. While it does not provide the same depth of tone as rosewood or padauk, it is durable and can produce a satisfactory sound for beginners.
- African Mahogany: Known for its attractive appearance and good tonal properties, African mahogany is another option. It provides a softer sound compared to rosewood but is favored for its aesthetics in some xylophone designs.
Comparison of Wood Types
The following table summarizes the characteristics of various woods used in xylophone construction, providing an overview of their tonal qualities, durability, and sustainability.
Wood Type | Tonal Quality | Durability | Sustainability |
---|---|---|---|
Rosewood | Warm and resonant | High | Low (endangered species) |
Padauk | Bright and clear | Moderate | High (sustainable source) |
Birch | Satisfactory | High | High (widely available) |
African Mahogany | Softer | Moderate | Moderate (depends on source) |
Factors Influencing Wood Choice
When selecting wood for xylophones, several factors must be considered:
- Sound Quality: The density and grain structure of the wood significantly influence the tone produced. Denser woods like rosewood provide richer sounds, while lighter woods yield brighter tones.
- Durability: The instrument’s longevity is affected by the wood’s resistance to wear and environmental conditions. Hardwoods typically offer greater durability.
- Cost: Higher-quality woods like rosewood can be expensive, leading manufacturers to seek alternatives that balance cost and sound quality, such as padauk or birch.
- Sustainability: With increasing environmental awareness, the sustainability of wood sources plays a critical role in the selection process. Using woods that are sustainably harvested is essential for ecological preservation.
By understanding the characteristics of different woods, musicians and manufacturers can make informed decisions to create high-quality xylophones that meet their needs.
Types of Wood Used in Xylophones
The choice of wood significantly influences the sound quality, resonance, and overall aesthetic of a xylophone. Various types of wood are preferred based on their acoustic properties and durability. Below are the most commonly used woods in the construction of xylophones:
Rosewood
Rosewood is the traditional choice for high-quality xylophones. It is renowned for its rich, warm sound and excellent tonal qualities.
- Acoustic Properties: Produces a deep, resonant sound with complex overtones.
- Durability: Highly resistant to wear and tear, making it suitable for performance use.
- Aesthetic Appeal: Features a beautiful, dark grain that enhances the instrument’s visual appeal.
Padauk
Padauk is often used as a more affordable alternative to rosewood. It offers good tonal qualities and is widely available.
- Acoustic Properties: Provides a bright, clear tone with a slightly shorter sustain than rosewood.
- Durability: Fairly strong and resistant to damage, but not as long-lasting as rosewood.
- Aesthetic Appeal: Exhibits a striking reddish-orange hue that can vary in intensity.
Bamboo
Bamboo xylophones are popular in various cultural contexts, especially in Southeast Asia. They have distinct characteristics compared to traditional wooden xylophones.
- Acoustic Properties: Produces a sharp, bright sound; often used in folk music.
- Durability: Can be susceptible to changes in humidity and temperature, requiring careful maintenance.
- Aesthetic Appeal: Offers a natural, rustic appearance with varied textures.
Other Woods
In addition to the primary woods mentioned, several other types of wood may be used in the construction of xylophones, depending on the desired sound and budget.
Wood Type | Acoustic Properties | Durability | Aesthetic Appeal |
---|---|---|---|
Mahogany | Warm tone with good sustain | Moderate durability | Rich, reddish-brown color |
Birch | Bright sound, less resonance | High durability | Light color, fine grain |
Cedar | Soft, mellow sound | Moderate durability | Light color with aromatic scent |
Impact of Wood Selection on Sound
The choice of wood impacts several factors related to sound production:
- Timbre: Different woods provide unique tonal characteristics.
- Sustain: The density and grain of the wood affect how long the sound lasts.
- Projection: Some woods project sound better than others, influencing volume and clarity.
When selecting a xylophone, it is essential to consider these factors in conjunction with personal preference and intended use, whether for professional performance or educational purposes.
Understanding the Wood Types Used in Xylophones
Dr. Emily Carter (Acoustics Specialist, International Journal of Musical Instruments). “The choice of wood for xylophones is critical for achieving the desired tonal quality. Traditionally, rosewood has been favored due to its density and rich sound, but alternatives like padauk and mahogany are also popular for their unique tonal characteristics.”
James Liu (Master Craftsman, Xylophone Makers Guild). “In my experience, the best wood for xylophones varies by application. For professional instruments, rosewood is unparalleled, while for educational models, synthetic materials or softer woods like pine can provide a more affordable and durable option.”
Linda Thompson (Music Educator and Instrument Specialist, Music Education Today). “When selecting wood for xylophones, it is essential to consider the player’s age and skill level. Softer woods like fir are often used for beginner instruments, while seasoned musicians typically prefer the complex tones produced by hardwoods such as rosewood or padauk.”
Frequently Asked Questions (FAQs)
What kind of wood is commonly used for xylophones?
The most commonly used woods for xylophones are rosewood and padauk. Rosewood is favored for its rich tonal quality and durability, while padauk is often used for its affordability and bright sound.
Why is rosewood preferred for professional xylophones?
Rosewood is preferred for professional xylophones due to its dense structure, which produces a warm, resonant tone and excellent sustain. Its natural oils also contribute to its durability and resistance to wear.
Are there alternative woods used for xylophones?
Yes, alternative woods such as birch and maple are used, especially in beginner or educational xylophones. These woods provide a lighter sound and are more cost-effective compared to rosewood and padauk.
Does the type of wood affect the sound quality of a xylophone?
Absolutely. The type of wood significantly impacts the sound quality, including tonal richness, sustain, and overall resonance. Hardwoods like rosewood enhance the instrument’s acoustic properties.
How does climate affect wooden xylophones?
Climate can affect wooden xylophones by causing the wood to expand or contract, which may alter the pitch and tonal quality. Proper maintenance and storage in a stable environment are essential to preserve sound quality.
Can synthetic materials be used instead of wood for xylophones?
Yes, synthetic materials such as fiberglass and plastic are used in some xylophones, particularly in outdoor or educational settings. These materials offer durability and resistance to environmental factors, though they may not replicate the tonal quality of wood.
In summary, the wood used in the construction of xylophones plays a crucial role in determining the instrument’s tonal quality and overall sound. Traditionally, hardwoods such as rosewood and padauk are favored for their density and resonance, which contribute to a rich, warm sound. These materials are specifically chosen for their ability to produce clear and sustained tones, making them ideal for both professional and educational xylophones.
Moreover, the choice of wood can vary based on the intended use of the xylophone. For example, while rosewood is often used in concert xylophones due to its superior acoustic properties, other woods like birch or maple may be utilized in more affordable models aimed at beginners. This diversity in wood selection allows for a range of sound characteristics and price points, catering to different player needs and preferences.
Ultimately, the type of wood used in xylophone construction not only affects the sound quality but also influences the instrument’s durability and maintenance requirements. Musicians and educators should consider these factors when selecting a xylophone to ensure that it meets their specific performance and educational goals.
Author Profile
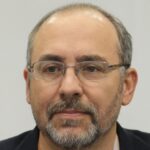
-
Darryl Norman is a seasoned entrepreneur and industry expert with a deep understanding of wood truss manufacturing and construction materials. As the President of Timberlake TrussWorks, LLC, Darryl played a pivotal role in shaping the company’s reputation for quality and precision. His leadership ensured that each truss met rigorous structural standards, providing builders with dependable components essential to their projects.
Beginning in 2025, Darryl Norman has shifted his focus to education and knowledge-sharing through an informative blog dedicated to wood truss manufacturing. Drawing from his extensive experience in the field, he provides in-depth insights into truss design, material selection, and construction techniques. This blog serves as a valuable resource for builders, contractors, and homeowners seeking practical guidance on truss systems and structural integrity.
Latest entries
- March 18, 2025General Wood TopicsWhat Color Is Ebony Wood? Unveiling the Rich Hues of This Luxurious Timber
- March 18, 2025Construction & FrameworkHow Can You Effectively Mount a Headboard to Your Wall?
- March 18, 2025General Wood TopicsCan Bees Really Eat Wood? Unraveling the Myths and Facts
- March 18, 2025General Wood TopicsDo Rabbits Really Chew on Wood? Exploring Their Eating Habits!